生産拠点として発展してきたベトナムで、精密加工にこだわる日系サプライヤーがある。彼らはどのような技術を持ち、この地のビジネスにつなげているのか。コア技術、製品、人材育成、ベトナムへの進出理由などを紹介する。
ボビンケースから油圧精密部品へ 進出25年の技術力・生産力
TOWA INDUSTRIAL(VIETNAM) Co.,Ltd.
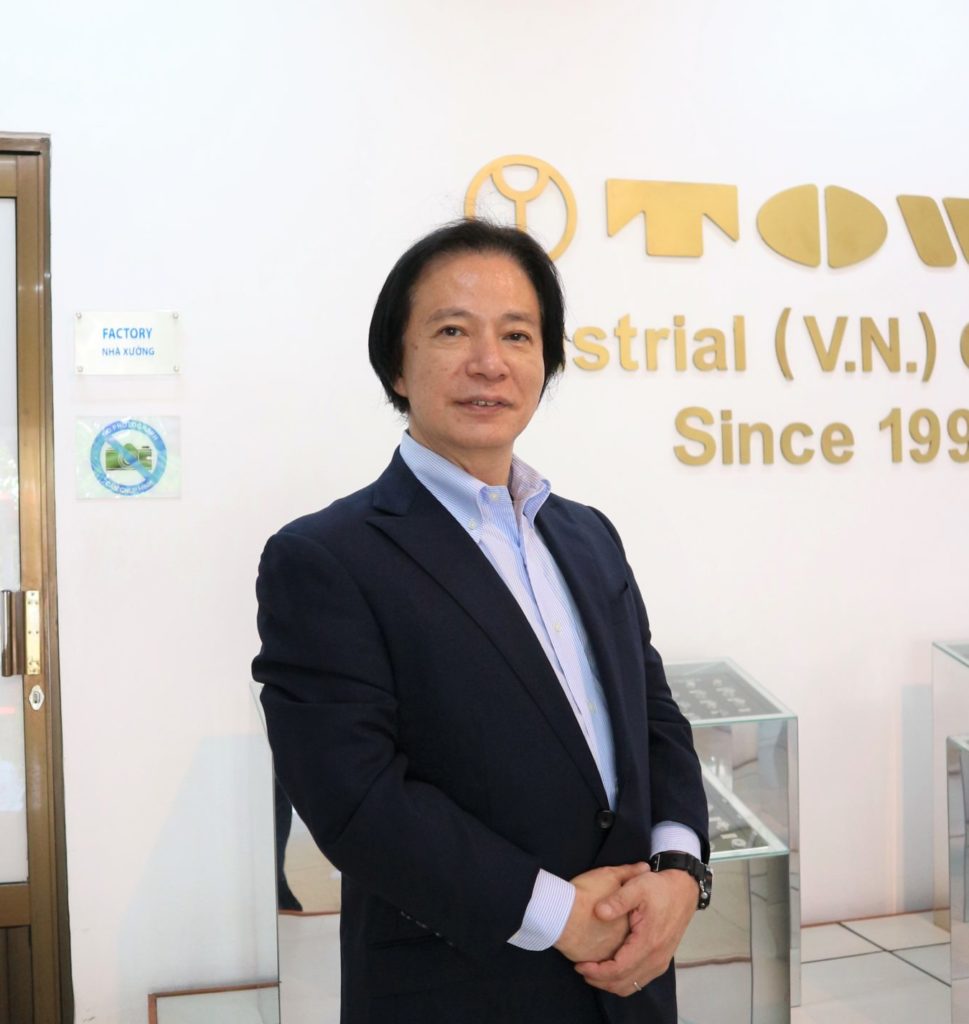
ピーク時の世界シェア7割 デバリングで油圧部品を受注
1995年にベトナムに進出し、来年で25周年を迎える東和インダストリアル(ベトナム)。新潟県のTOWA JAPANが親会社だが、渡邉氏は両社のトップを兼務しており、現在の生産能力はベトナムが日本の約10倍へと拡大した。
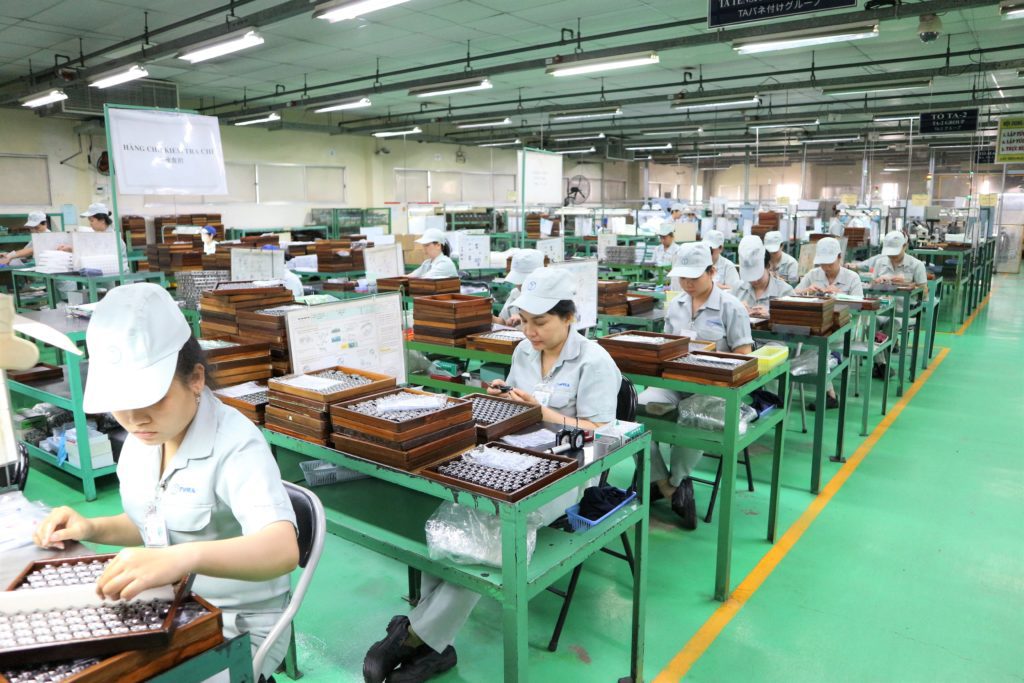
1996年にホーチミン市で操業を開始し、第2工場、第3工場を竣工。3工場がフル稼働となったため、今年9月には南部ビンロン省にサザンスター工場を新設。来年1月に操業開始予定で、生産能力を全体で約3割増やす計画だ。
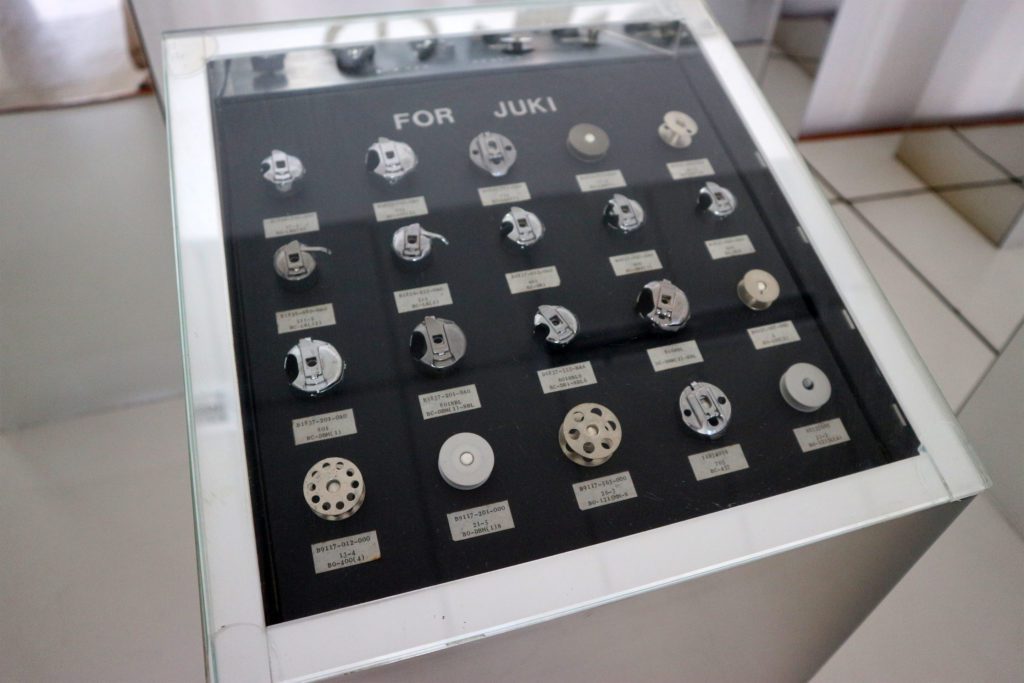
同社の主力製品は産業用ミシンで使われるボビンケース。アパレルの縫製業で使われる一般的なもの以外に、靴、ベルト、カーシートなど皮革製品用ミシンの特殊なボビンケースも生産しており、ニッチ製品では手術で心臓を縫合するための医療機器向けもある。
もうひとつは油圧部品の精密加工で、きっかけはベトナム進出前に東京の技術展に出展したこと。当時既にボビンケースで世界シェア約7割だったが、逆にこれ以上の伸びはあまり期待できないと判断。精密加工部品を数万個単位で大量生産できる技術力、特に油圧部品で必須となる微細なバリを取る、マイクロデバリングの技術が活かせると考えた。
「バリがあると油圧製品がうまく動かなくなるように、ボビンケースでのバリはミシンの糸を切ってしまいます。どちらも高品質な穴あけ技術が欠かせないのです」
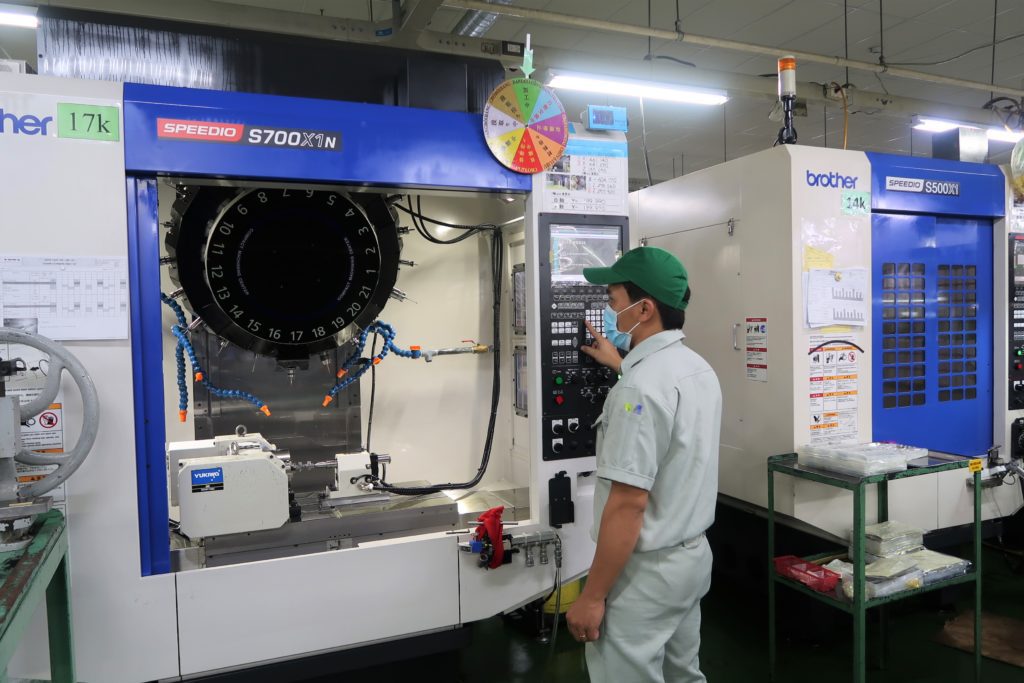
受注したのは自動車のアンチロックブレーキシステム(ABS)で使われる、油圧式フローコントロールバルブの生産。技術の応用は以前から社内でトライしており、ABSの他にも光ファイバー用のコネクタやマイクロエンジンなども試みたそうだ。
ここから顧客の業界が広がり、現在では自動車だけでなく新幹線の油圧ブレーキの部品、建設機械、農業機械、工作機械などの油圧部品、マリンエンジンの旋回モーター用部品などを生産している。顧客からの図面通りに作るだけではなく、機能性の向上やコストダウンの提案も行う。
「売上ベースで現在はボビンケースが40%、油圧など他の分野が60%ほどと逆転しています」
第1工場では一般的なボビンケース、第2工場では特殊なボビンケースと自動化機械を自社開発する生産技術部門、第3工場では油圧部品が中心だ。ビンロン省の第4工場はホーチミン市の分工場という位置付けで、ボビンケースと油圧部品の両方を生産。稼働中の第1~第3工場には合計約800人の社員で生産に当たり、操業準備の第4工場では現在約100人の新規採用者の研修に入っている。
品質管理のシステムを構築 技術力を支える品質保証
こう書くと、精密加工に特化した中小企業が技術力を横展開させたと思われがち。しかし、単純な話でないのは、ボビンケースと油圧部品では生産プロセスが多少異なる点だ。機械加工後のボビンケースは手作業で組み立てる。自動化できないほど機構が複雑なためで、実際にベトナム進出の理由の一つは、日本での職人の減少と人件費の安さだった。
一方、油圧部品は機械化による大量生産で、人手を極力省いた精密加工の自動化を目指す。この精度1000分の2~4mmでの量産を実現する同社の強みが、独自のシステムによる品質管理だ。ボビンケースもそうだが、どれだけ歩留まりを良くして、コストを下げるか。そのために設備、カッター、油などを選定し、ラインを考え、設備投資を繰り返す。
「離職率が高いベトナムでは、『担当者が変わっても品質を保つ』という仕組みも必要になります」
もう一つ大切なのは測定技術で、精密加工部品の安定生産には正確な測定とデータ解析が必要となる。上述のデバリングもそうだが、人の目に見えないミクロン単位を電子顕微鏡で測定し、問題を発見して次の製品へとつなげていく。
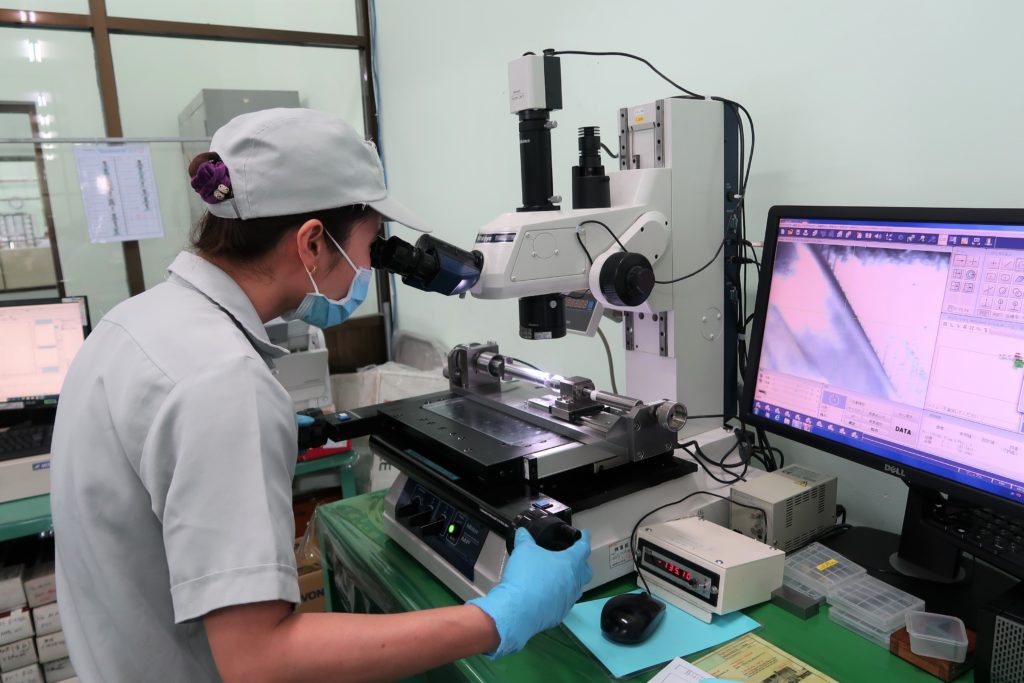
同社の職位は社長と副社長以下に、部長クラスのマネジャー、副マネジャー、アシスタントマネジャーがおり、彼らが生産計画を作り、品質管理も担当する。その下が課長クラスのセクションチーフ、アシスタントセクションチーフがおり、日々の生産を管理する。その下は班長のグループリーダー、サブグループリーダー、エンジニアとなる。
「生産システムは日本方式を採用しています。品質管理のISOは当然取得し、弊社は日本で2番目にデミング賞(総合品質管理における世界最高ランクの賞)を授賞した中小企業です。加工の難易度が高い部品を選んでもいて、品質管理には自信があります」
ボビンケースも油圧部品も顧客数は増加しており、日本と近隣諸国への輸出がほとんど。ただ、ベトナム国内に納品するケースは少ないものの伸びている。中国からの工場の移転増も理由と見ているが、顧客は外資系企業だ。
「ベトナムのメーカーはまだ、2~3ミクロンという加工精度を求めていないのでしょう。今後は拡販させたく、『プラスワンでのベトナム生産』というセールスポイントを使った営業も進めたいですね」
日本でR&D、ベトナムで大量生産 精密加工業が気を付けること
親会社は今年で設立70周年を迎え、昨年はその社名を東和製作所からTOWA JAPANに変更。日本本社というより、ベトナムと対等なポジションとなった。今後は日本を一層R&Dの拠点とし、ベトナムでの生産増を目指す。そのためにもサザンスター工場を竣工させた。
当初は手作業での組立てを目的とし、安定が見込めると徐々に設備投資を進めて、人を育てながら生産量を増やしてきた。そんな中小企業の成功者からのベトナム進出のアドバイスは、まずは本社の体力を考えて進出を判断すべきという。
精密加工には設備投資が必要なので、初期投資が高額になり、回収するまで時間が掛かる。ある程度の余裕がないと撤退の危険性も出てくる。次に一定以上の事業規模が見込めること。今では資本が少ないと人材の採用は困難で、小規模な人海戦術では事業の伸びは期待できないからだ。そして、同業他社との競争は激しくなっている。
「日系もそうですが、台湾や韓国に加えて中国、数は少ないものの欧米などの外資系企業、成長著しいベトナム企業も侮れません。この狭いベトナムで世界競争に参入することになります」
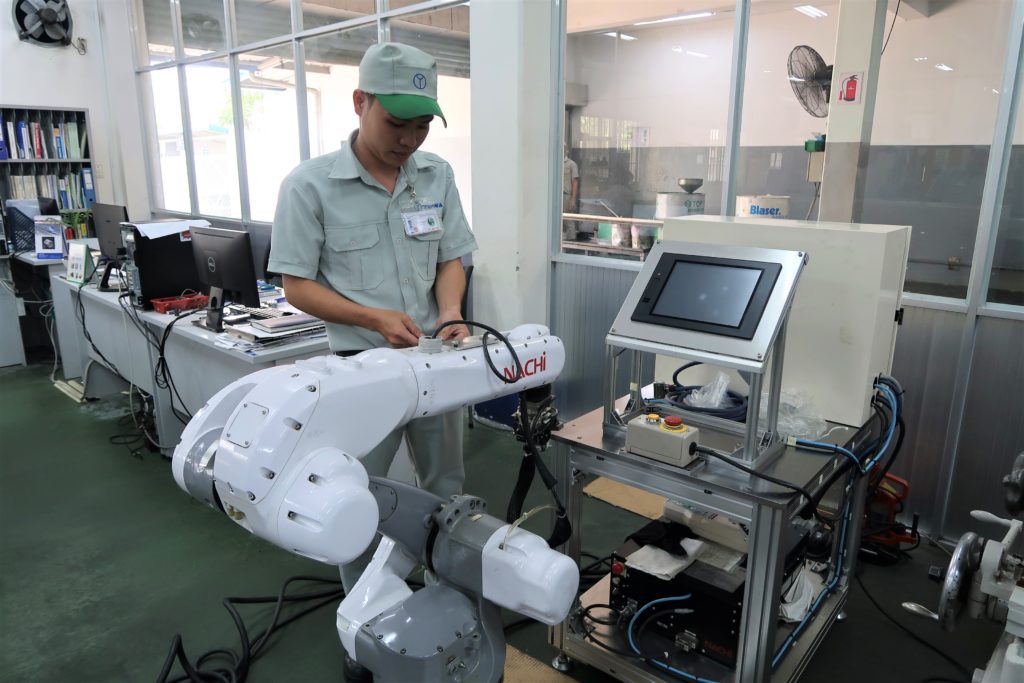
メインは二輪・四輪用ランプ 「鏡面ミガキ」の技能を伝承
MEISEI VIETNAM CO.,LTD
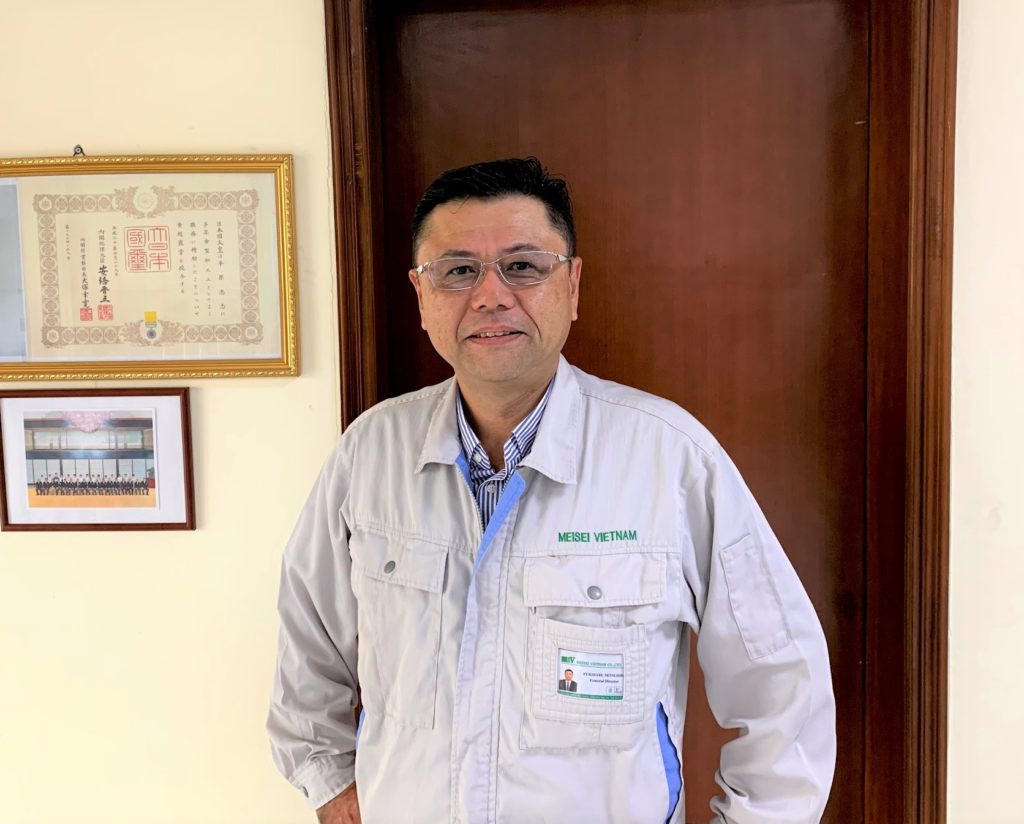
General Director
吹春光浩氏
機械加工と手作業の強み ベトナム人技能者を育成
「MEISEI」で知られる株式会社名古屋精密金型。二輪・四輪用のヘッドランプやテールランプの金型製作を得意とし、大手ランプメーカーなどの幅広い顧客を持つ。そのベトナム拠点として2004年に設立されたのがメイセイベトナムだ。
これらランプの金型には高い精度が要求される。電球やLEDなどの光源から光を精度よく反射させる反射面と、光を歪ませずに通過させるためのレンズといわれる意匠面があり、レンズの金型には均一した肉厚と「鏡面ミガキ」の精度が必要になるからだ。
精密な機械加工で仕上げた面に、さらに手作業で鏡のように磨き上げる。しかも、透明な製品の場合は表と裏に精度が必要となるため、金型のキャビティ(凹部)とコア(凸部)の両面が対象となって難易度が増す。磨き上げるまでにはヘッドランプで3~4週間かかるそうだ。
「鉄を削って、手で磨く。ランプの精密金型で培われたデジタルの機械加工とアナログの手作業、その伝承が弊社の強みです。ベトナム人材を確保し、何年もの間、根気よく技術を教えてきました」
特に金型の仕上げやミガキでは、日本での技術研修に繰り返し参加させ、『現代の名工』に選ばれた社員による指導教育も行ってきた。
ミガキで難しいことはまず、機械加工した面を崩さないこと。面がだれたり、磨きすぎてくぼんでもいけない。次は傷をなくす。磨くとどうしても凹凸の「磨き筋」が付くので、筋がなくなるまで番手を細かなものに変えながら、最終的に鏡面にしていく。使うのは砥石、研磨ペーパー、ダイヤモンドペーストで、それぞれ数種類がある。

「鏡面に磨けるまで10年はかかるでしょう。現在のミガキのスタッフは15名おり、14人が女性です。日本でも通用するような技能者で、定期的な社内転勤で1年ほど日本に行き、研修だけでなく現場の手伝いもしています」
現在は育ったベトナム人が若手を教えており、離職率は非常に低い。彼らの技術を学びたい気持ちが強いのと、ビンフック省という土地柄で地元の人が多く、家族や親戚が就職を勧めることも増えたという。
同社の技術部署は設計、製造、メンテナンスに分かれ、設計は図面の作成とプログラムを組むCAMの部隊、製造は機械加工、金型仕上げ、ミガキで、メンテナンスは他社製作の金型の修理も行う。
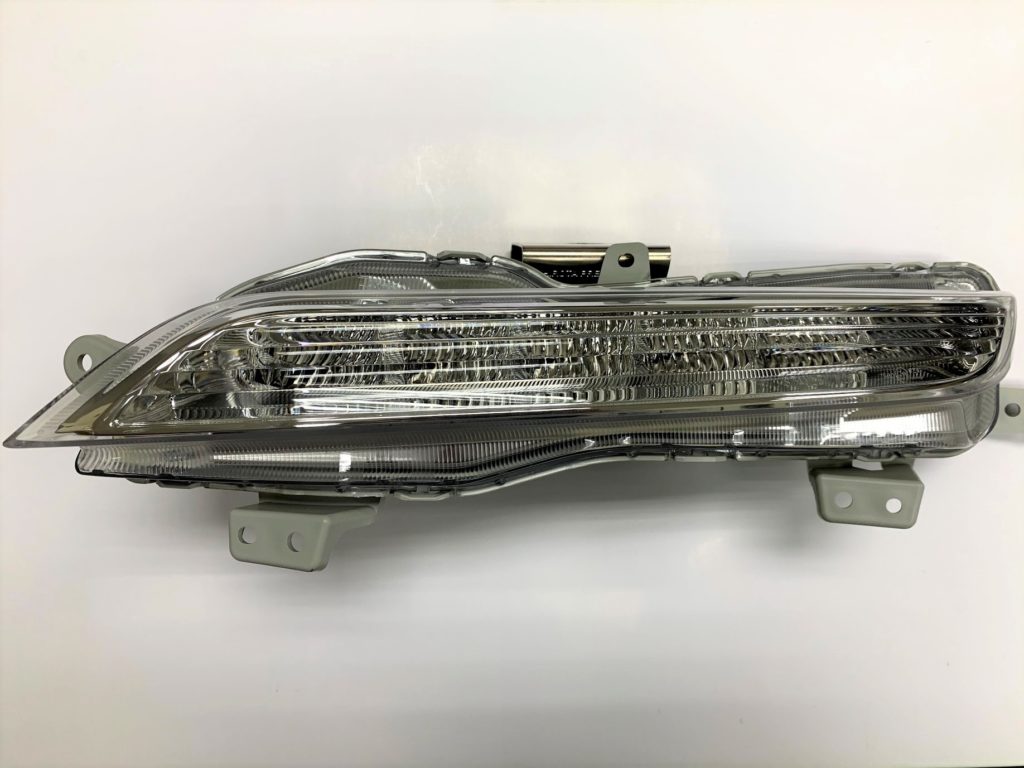
ローカル金型メーカーが増加 デザインと安全では日系優位
メイセイベトナムの金型は主に二輪、そして四輪のヘッドランプとテールランプで、二輪のサイドカバーやハンドルカバーなどの樹脂成形金型、エンジン関連のダイキャスト金型も作る。金型の重量は10tまで対応可能で、年間で約80型を生産している。
顧客は日系企業がほとんどだ。2012年くらいまではベトナム国内から発注が多かったが、ランプメーカーが日本での内製化を進めたため、日本本社からの依頼が増えた。こうした金型の輸出は現在4割程度で、残りはランプに限らずベトナム国内向けとなっている。
「進出当時、ローカルの金型メーカーはほぼなく、日系企業も数社程度でした。設立の早さも仕事を受注できた理由だと思います」
ベトナムを選んだ理由は人件費の安さ、親日と勤勉さ、既に進出していた大手企業の後押しなどで、当時の社長が2001年に視察し、帰りの飛行機内で決断したという。そして創業から15年。事業は順調に進んできたが、進出当時との変化もある。それはローカルの金型メーカーが育ち、増加していること。彼らは低価格で勝負しており、受注もしている。そのため当時より仕事が分散しているそうだ。

「日系企業を退職して起業した人が多いようです。こうした金型メーカーを選ぶ企業もありますが、デザイン性の高いもの、安全性が必要な部品などでは日系が選ばれています。弊社に限らず、日系金型メーカーの技術力は総じて高いですから」
販路の拡大も続けている。特に新規に進出した、あるいは進出の準備している製造業などだ。ベトナムでの顧客には金型をよく知る技術者が少なく、同社のような金型メーカーに頼ることも多々あるそうだ。
「その際には技術的な提案が不可欠です。お客様に信頼していただく提案力と技術力で、金型技術を認知していただく営業を続けています」
四輪用への設備投資 金型業界の底上げに尽力
吹春氏がベトナムに来て1年と数ヶ月が過ぎた。これから取り組みたいのは金型の大型化であり、大型部品を受注するための設備を増したいと語る。中でも今後のベトナムでニーズが高まるだろう、四輪用の部品だ。そもそも日本本社は四輪用ランプの金型が主業務であり、主要な大手メーカーに納入している。
「例えば、日本から受注した金型をベトナムで製作し続け、実績を重ねれば、ベトナム国内での新しい四輪に対応できると思います。同じ北部ではビンファストが四輪の生産を始めました。加工機はあるのですが数が少ないので、まずはこちらの設備を増やしたいですね」
ハノイには日系だけでなくローカルメーカーも多数加盟する、「日越金型クラブ」という団体がある。金型メーカーと関連部品メーカーが100社ほど集まっており、同社もそのメンバーだ。ベトナム国内で金型の認知度を高めること、技術力の向上を図ること、そして世界で注目される産業となるように業界の底上げを図っている。
「こうした活動を続けていくことも、ベトナムで仕事をさせてもらっている私たちの役目だと感じています」
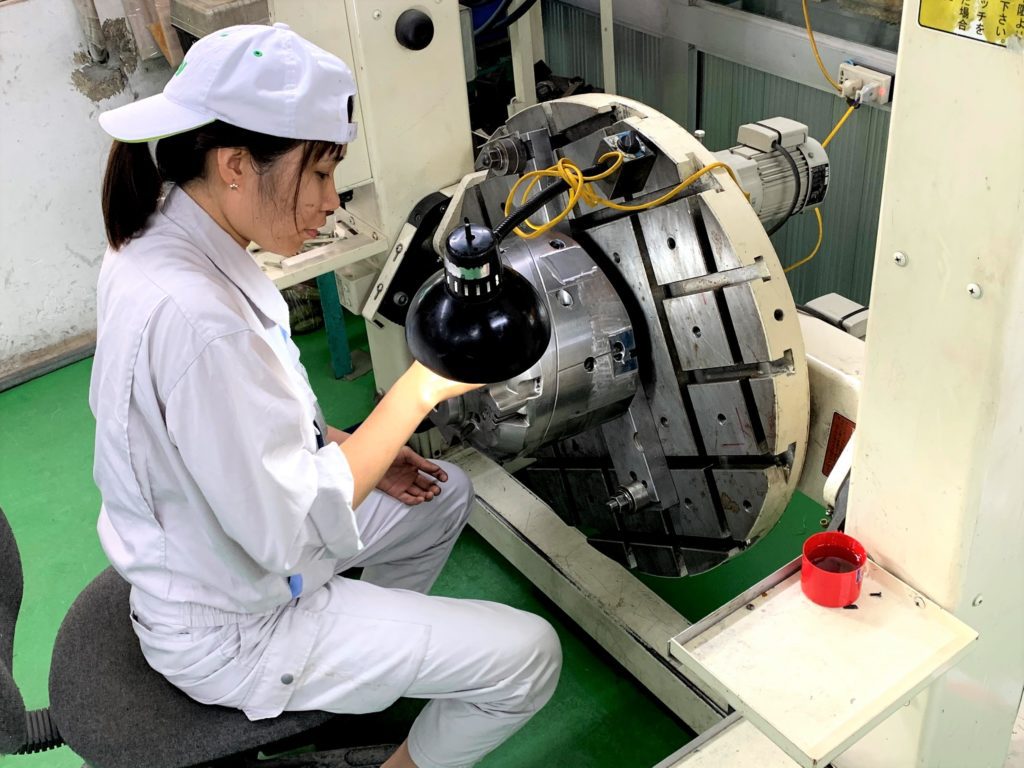
金型から成形まで自社生産 光学機器で培った精密加工
CAM PLAS MOULD (VIETNAM) CO.,LTD.
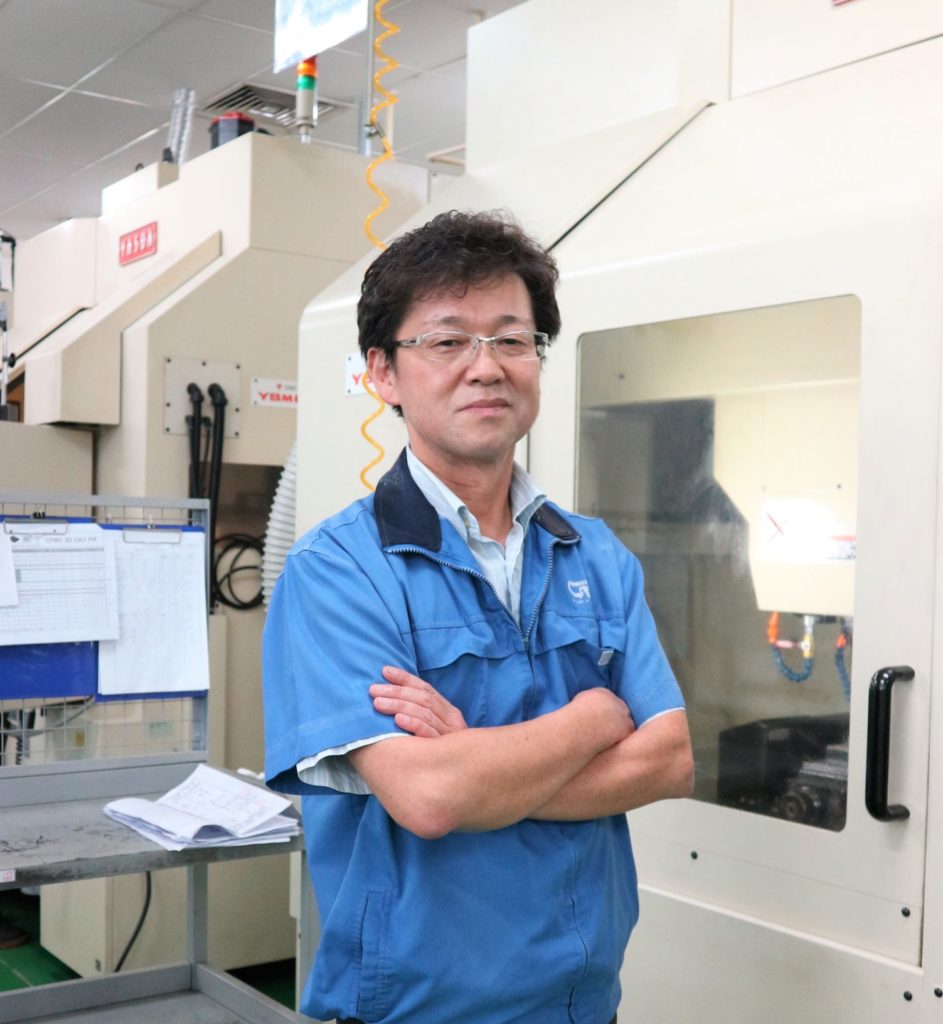
General Director
長 克彦氏
金型製作から精密成形へ 外資系企業への拡販を
栃木県にある株式会社キャムは、光学機器の部品から精密プラスチック成形の技術を磨いてきた。成形用の金型も自社で製作する一貫体制で、鏡筒などカメラのレンズ周りの部品で拡販を図り、現在はその技術力の応用で情報機器、事務機部品、パソコン用記憶媒体、車載用のリチウムイオンバッテリー、エアコン関連の部品など、多種多様な製品を製作・販売している。
海外進出は比較的早く、1995年に海外初拠点をシンガポールに設立。その後は取引先企業の海外進出もあって積極的に海外展開を推進した。香港、中国の上海や東莞、タイなどと続き、ベトナムにはキャムプラスモールド(ベトナム)として2007年に進出。現在は日本を含めて生産拠点が世界に工場8ヶ所、営業拠点が4ヶ所ある。
「当初ベトナム工場は、各国の量産拠点に供給する、金型の生産工場として設立されました。金型の技術力を根付かせるのが目的で、当時の南部では、精密成型部品のニーズは少ない状況でした」
市場の変化で成形機を導入し、プラスチック成形をスタートさせたのが2016年。既存顧客に合わせての稼働ではないため、市場開拓から始めたが、外部顧客から期待度が高い印象を受けたそうだ。
ベトナムでは難度の高い精密部品の生産先はまだ少なく、輸入が多い。これが商機となる。同社は設計から金型製作、成形まで対応が可能で、一貫したモノづくりを現地でできることが魅力になると考えたのだ。
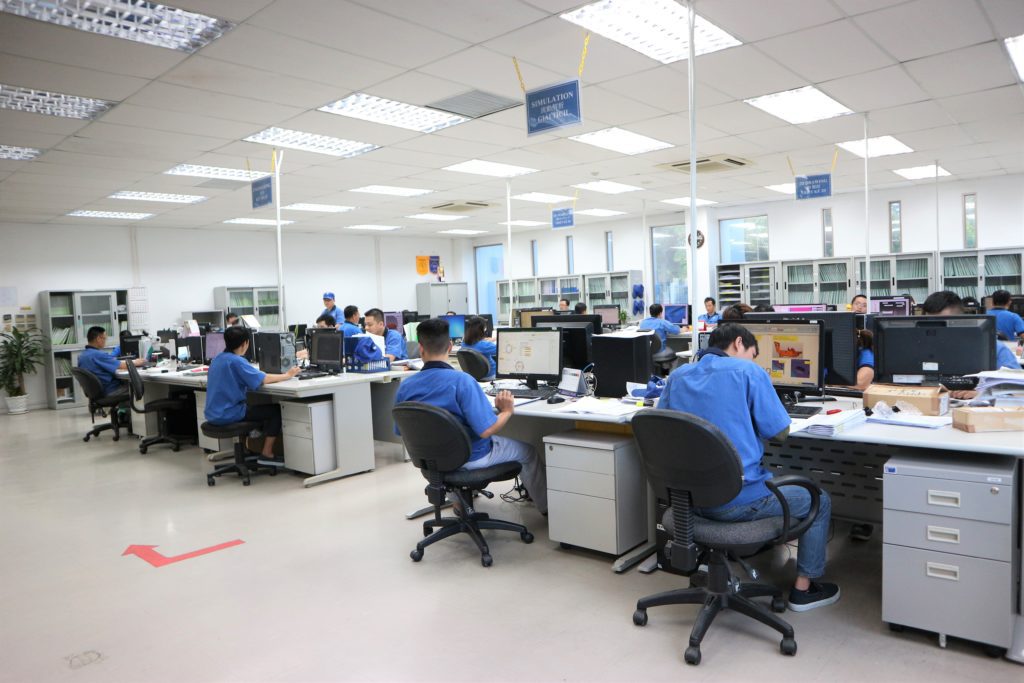
「市場での競争には蓄積した技術力を活かして、品質、コスト、納期でお客様にご満足いただける製品を提供できると思いました」
現在は電気系メーカーや自動車関連メーカーなど顧客はすべて日系企業で、成形機導入をきっかけに声がかかることも多い。また、欧米メーカーの視察や、米中貿易摩戦争で中国からの工場移転が進んでいるので、ターゲットとする部品を決めて外資系企業にも拡販したいと考えている。
「既存の建屋に成型ラインを増設しましたが、工場の裏手に敷地は確保しており、将来はそこに成形工場を増設しようと計画しています」
流動解析でリスクを軽減 3部署は24時間体制
同社の特徴は複雑な形状の樹脂成形ができること。また、精密ギヤなども得意で、従来の射出成型では困難だった形状も金型構造の工夫により可能とした。ギアは業界を問わずニーズがあり、高精度品の需要は増加傾向にあるそうだ。
もうひとつの特徴と呼べるのが、生産前に行う樹脂の流動解析やCAE解析。顧客からの要求を基にしてシュミレーションを実施し、金型構造を決定している。
「製品の品質を確保するために過去の実績を蓄積し、データ化することで設計に活かしています。部品の高度化は弊社にとってチャンスととらえています」
同社の設計、金型、品証の3部署は、3交代の24時間体制を取っている。これは連携したインからアウトまでの一貫体制で顧客ニーズに応えるためだ。また、製造した部品は製作者自身で評価した後に、品証でも再度評価している。人手とコストが必要だが、精度確保には必要な手段であると考えている。
「金型の製作期間は半年、1年を掛けた長期的な日程を要していましたが、最近では短納期が進んでおり、部品次第ですが1週間でお受けするケースもあります。24時間の対応は必要不可欠な顧客ニーズとなっています」
本社も自社も自動機を開発 ワーカーでなく技能者を
株式会社キャムが推進しているのが自動化であり、積極的に自社開発をしている。キャムプラスモールド(ベトナム)も同様で、日本本社が制作した自動機を導入して活用している。同社のロット数は100~200万個と幅広く、小ロット品の自動化は厳しいが、生産量や品質確保には自動化設備が適しているそうだ。
同社ではレンズ周りの部品の検査に自動機を導入し、復数のカメラで品質をチェック。人による検査のバラツキを抑えて、品質が安定するという。また、日本で開発したドライカラーパウダーの自動供給装置は、成形機上で原材料に着色が可能。成形品に正確な色が付けられるので市販もしている。
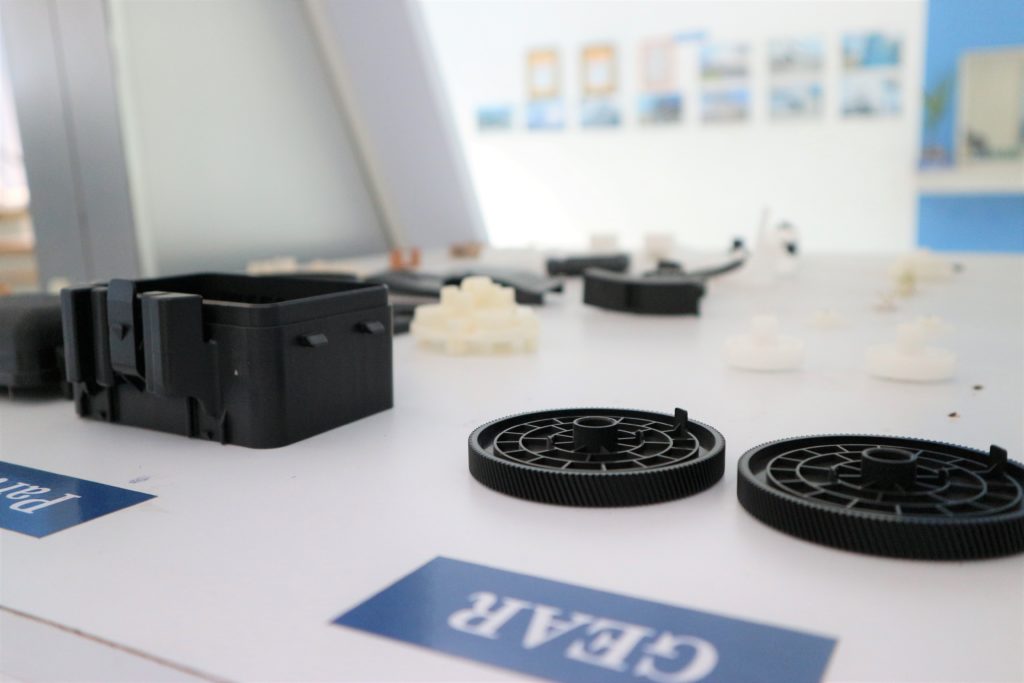
「ベトナム人の労力で人海戦術的な仕事をする製造業もありますが、弊社はワーカーではなく金型工作技術や成形技術の技能者を育てています。そのため、現場はできるだけ自動化したいと考えています。また、日本に研修制度があり、日本で一定期間実務を行って人材を育成しています」
ベトナムでも昨今は賃金上昇が顕著だが、今はまだ自動化に投資をしてもさほど効果は得られない。しかし、いずれは賃金高騰による労務リスクが出てくると見ており、そのために布石を打とうと考えている。
「今後、ベトナムには大きなチャンスがあると確信しています」