ベトナムで生産しているちょっとニッチな商品を取材! 市場にあまりないモノづくりの、材料・部品の調達は? 工場スタッフの教育は? 月産数はどのくらい? 国内販売しているの? そもそもなぜベトナムに?
YAMATO PROTEC VIETNAM
消火器 高品質な日本の国家検定商品
その価値が分かる企業に浸透中
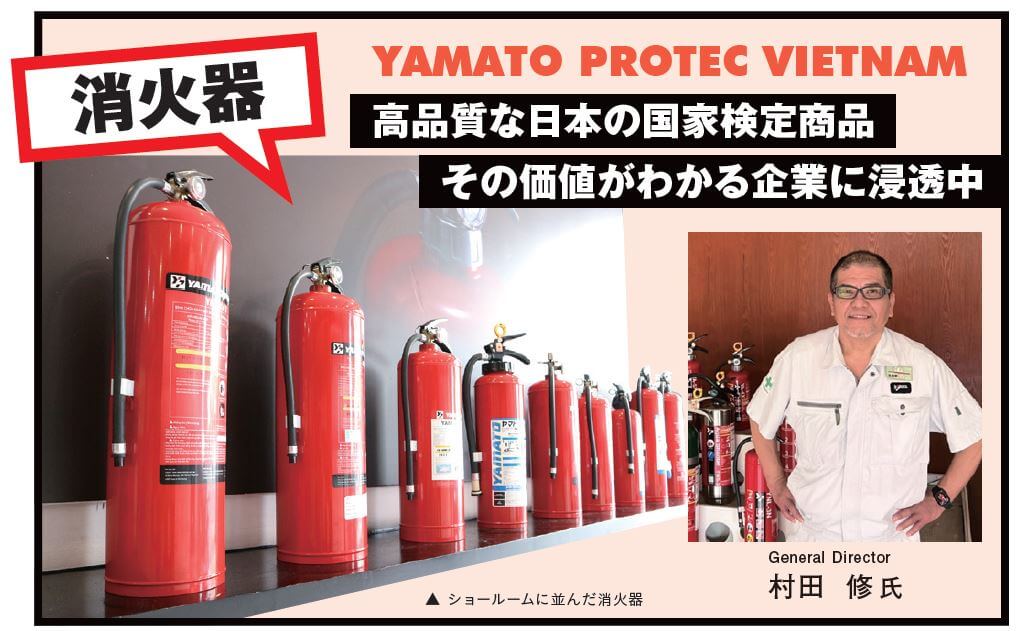
初の海外工場がベトナム
国内販売が10年で3割に
ヤマトプロテックは1918年の創業以来、化学泡消火剤や、現在広く使われているA(普通火災)、B(油)、C(電気)に対応するABC粉末消火器を発明し、消火器の製造販売だけでなく消火設備の施工なども請け負う。
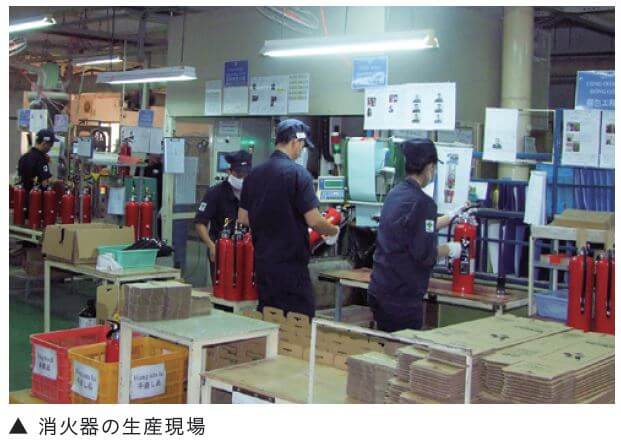
2000年から海外に第2の生産拠点を持とうと動き始め、アジアの候補地を視察する中でベトナムに決めた。2003年にヤマトプロテックベトナムをビンズン省に設立して消火器の生産を開始。消火器には粉末、強化液、泡の大きく3種類があり、日本向けにABC粉末消火器の20型1機種のみを輸出している。薬剤量6kgの大型タイプで、月産で3000本程度になる。
ベトナム工場の立ち上げに携わり、2016年から再赴任をしている村田氏は語る。
「消火器は日本の消防法による国家検定に合格しないと販売できません。そのため社内規定として現地調達できないものがあります」
例えば、消火剤を発泡させるための金属部品が国家検定商品なので、形状や材料を変更できない。本社で図面を確認して日本から輸出しており、薬剤も全て日本からの輸入だ。こうした部材、薬剤、塗料などの輸入品が全体の約20%、残り約80%となる鉄板、樹脂、梱包資材などは現地調達している。
2013年からは国内販売を始め、粉末と強化液の消火器を約8種類生産。販路はローカルの代理店経由で大きな拠点はハノイ、ダナン、ホーチミン市に合計5つあり、そこから小売店に卸している。
「お客様は企業が多く、売れ筋は一般的な4㎏タイプ、工場などでは6㎏や8㎏の引合いもあります」
ベトナムも日本と同様に消防法に基づいた消火区画があり、対象となる平米数などで消火器のサイズが変わる。そのため、ラインナップを日本と変更する場合があり、ベトナムの消防法による検定に合格する必要もある。
国内向けの生産は年々増えて1年に2万本程度となり、全生産量のうち約30%にまで高まった。
「タイには販社、インドネシアには協力企業の販社があり、両国にも輸出しています。ただ、発注を受けての輸出ですので、定期販売ではないです」
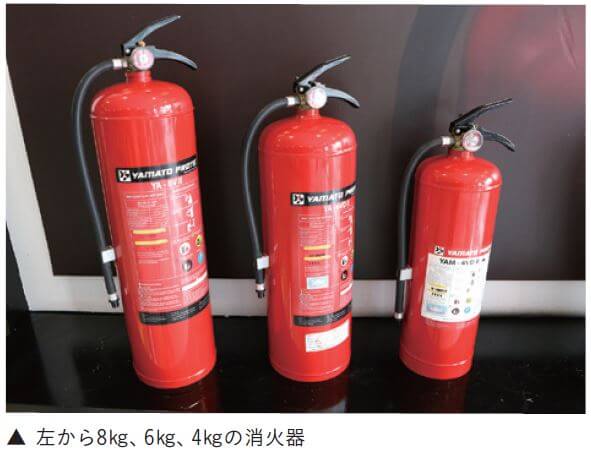
火が消えない消火器も市場に
鉄板1枚からの一気通貫生産
国内販売用にも日本から輸入した部材や薬剤を使用しているため、日本と同品質の消火器となっている。これが高付加価値を生んでいるわけだが、競合となる消火器メーカーはベトナム企業が数社あり、大抵が中国から本体容器(ボトル)と薬剤を輸入して詰めているそうだ。中国から消火器を輸入する企業もあり、これらを合わせて市場の90%程度を占めているという。
「消火試験をする際は自社製品以外に他社の消火器も試すのですが、ベトナム製や中国製は火が消えにくいのです。薬剤も原料の配分も違うのでしょう」
他社の価格は同社の半値程度という場合もあるが、こうした競合は意識していない。日系企業を含めた価値がわかる法人顧客が対象だからだ。天災や火事が多い日本では防災への意識が高いが、火災が比較的少ないベトナムではその認識が薄いと村田氏は語る。だから消火器は一般家庭まで普及していない。
ヤマトプロテックは一気通貫の生産体制が特徴であり、ベトナムでも同様だ。消火器の生産工程を簡単に言うと、鉄板を寸法に合わせて切断し、ロール状にして溶接し、本体容器を作る。それに表面処理をして、粉体塗装と焼き付けをする。内部に部品を取り付けて薬剤を充填し、外部にはレバー、ホース、ノズルなどを取り付ける。漏れなどの各種検査をして完成。梱包して出荷する。
「鉄板1枚から作る一気通貫の生産はほかに知りません。ベトナムで弊社だけだと思います」
特殊な製品なので作業担当者の入れ替わりが激しいと品質にムラが出てしまうため、退職者を出さないように福利厚生を手厚くし、給与や手当も考慮している。そのためか離職率は低く、同品質の消火器が長く生産できているという。仕事ができるまでには塗装などの1工程で3ヶ月ほど、全ての工程で1年弱がかかる。。
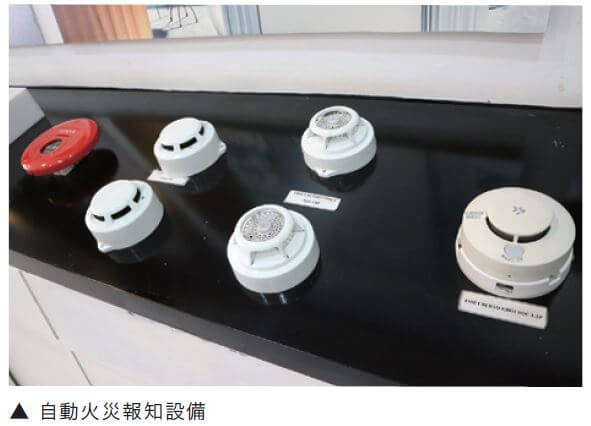
消火器5機種を新たに生産
2つの現法の統合を予定
国内販売は右肩上りで伸びている。今後も強化する予定で、工場などを建設する日系のゼネコンやサブコンからの引合いも多い。また、泡消火設備や二酸化炭素消火設備などの消火設備も手掛けており、日本から輸入した設備で施工している。
日本向け輸出では今年から新しい消火器の生産を始める。第3四半期からスタートして年間で2万本ほどを計画しており、およその年間生産数は3万6000本から5万7000本に増える。
製品は現在日本で生産している船舶用の消火器5機種。鉄板を溶接、塗装して薬剤を充填するベトナムでの製法は、いわば古いタイプの作り方で、日本での需要は減っている。海外モデルとの棲み分けとしてある3ピース容器船舶用消火器がこの製法なので、ベトナムに移管するのだ。
2007年には第2工場として、ヤマトプロテックドンナイをドンナイ省に設立した。こちらは消火器ではなく、火災の際などに使う避難設備を日本向けに生産している。マンションのベランダにあるような避難用の梯子で、ハッチを開けると畳まれた梯子が下方に伸びるような仕組みだ。ベトナム国内販売はしていない。
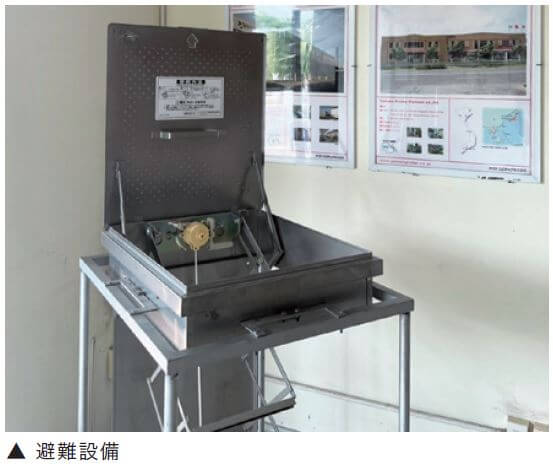
「こちらは別会社から従業員ごと引き継いだので現地法人が2つになりましたが、これから2社を1社に統合する予定です。従業員は合計で約100人になり、今まで以上にベトナム事業を伸ばしたいと思っています」
DAIGAKU (VIETNAM)
額縁 当地でしか作れないプレミアム商品
賞状、葬儀、ジグソーパズル用も
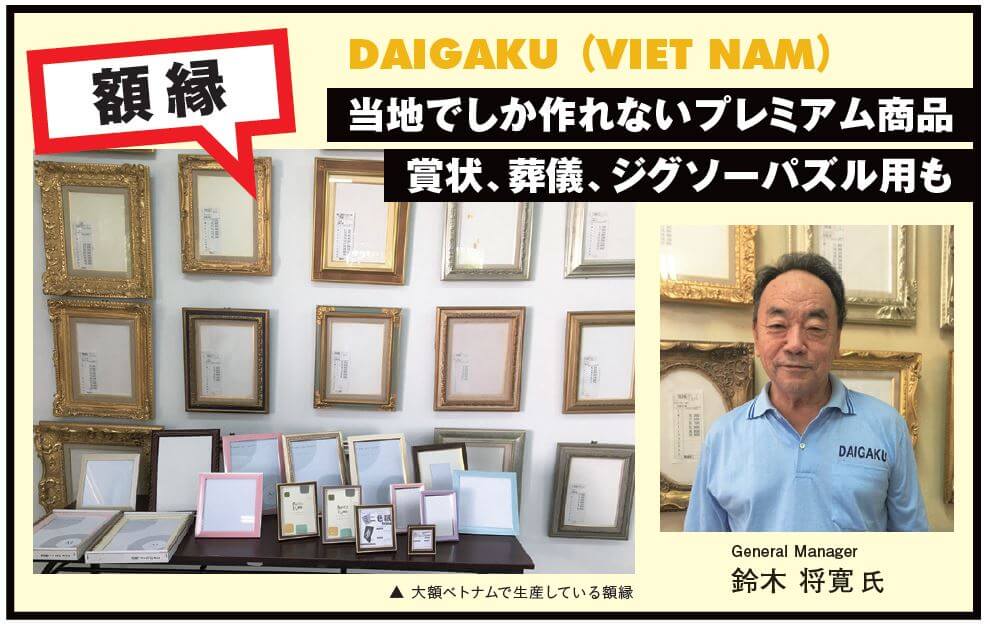
ベトナム人の「目」が決め手
全工程ができるまで30年
1957年創業の大阪府の額縁メーカー、大額。海外初の生産拠点となったのが2008年設立の大額ベトナムだ。
以前は日本工場のほか、中国やタイの工場に生産を委託。「モールディング」と呼ばれる装飾を施した額縁用の長い竿(木材)、額縁用のパーツや付属品などを輸入していたが、特に中国の価格や人件費の上昇で新たな生産拠点が求められた。
ベトナムを選んだ理由は安価な人件費、外資100%での設立、決め手となったのは「ベトナム人の色を見る目」だった。額縁職人を45年続けてきた鈴木氏は語る。
「フランス文化の影響なのでしょうが、彼らは白や黒の中の差を見分けることができます。私はタイでも指導していましたが、タイ人は青みや黄色が入った白でも同じ白に見え、ベトナム人は区別できるのです」
この「目」は特に塗装の工程で活躍する。多様な顔料を組み合わせて塗料を作るが、機械でレシピ通りに混ぜても同じ色が出るとは限らない。その際の配合の調整(調色)に役立つのだ。それでも1人前になるまでに5年かかるという
日本工場と同様に原木からの一貫生産。工程を簡単に説明すると、購入した木材を切断して図面に合わせて削り、コーティングをして、額縁のサイズに機械でカット。1辺ずつ隙間なく合わせて四角に組み立て、紙やすりで丁寧に研磨する。
ムラなく塗装して、その上に金箔や銀箔を1枚1枚丁寧に手貼りし、出来上がった額縁を検品する。数十種類ある額縁のサイズに合わせて段ボールをカットして箱を製作。
最後は仕込みで、アクリルやガラスをカットして額の内部に入れ込み、裏面には緑の紙を貼り、金具を付けて仕上げる。日本でそのまま販売できる完成品だ。
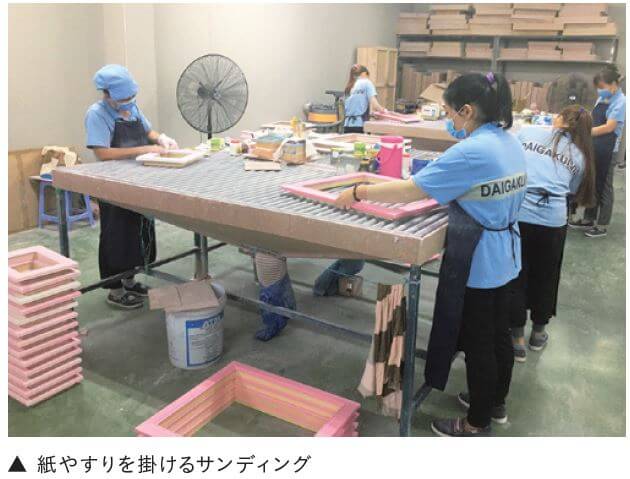
「私は全ての工程ができますが、一貫してできるまで30年くらい。それは難しいので工程を分けて指導しています」
美術館に飾られるような超高級品には手彫りの作業が加わる。経験者を採用しているが仏像や仏壇を対象としていた者がほとんどなので、3年に1回は日本に派遣し、ヨーロッパ仕様の額縁などを見学させている。
「こうした額縁がベトナムにないからです。本当はヨーロッパに行かせたいのですが(笑)」
日本の技術をベトナムに移転
モノづくりを楽しめるかがカギ
「額縁」と聞いて何が入った額を想像するだろうか。日本で大額が一番多く販売しているのは表彰状や卒業証書などの賞状を入れる賞状額、2番目は葬儀で遺影を飾る葬儀額、3番目は完成したジグソーパズル用の額縁だ。
「4番目は油絵や水彩など絵画用の額縁でしょうか。ただ、価格は賞状額の10倍も珍しくないので、売上ベースだとかなり増えます」
絵画額はデザイン、色、サイズなどで多種多様にあり、その数は50万アイテム以上。このうち毎月7000アイテムほどを生産している。日本では既定のサイズが多いが、多くの国では写真立てなど小さいサイズ以外はオーダーメイドが一般的とのことだ。
生産量は1週間に40フィートコンテナで1本~1本半を日本に輸出。完成品以外にモールディングや部材なども含まれ、日本本社だけでなく納品した額縁店がカットや組立てをするケースがある。
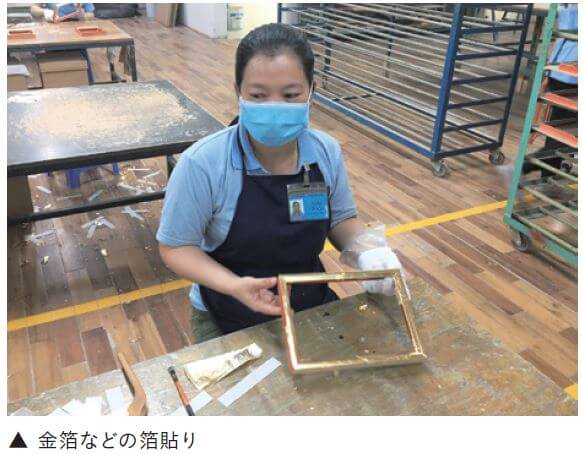
「日本の商品の売上ベースで完成品は25%、モールディングやパーツを含めると35%ほどになります」
機械化できる大ロットの商品は日本で生産し、手作業の多いベトナムでは多品種小ロットのプレミアム商品が主力だ。絵画用の高級額のように手間が掛かって値段の張る額縁で、既に日本では彫刻や箔貼りの職人が希少になっており、そのため高度な技術をベトナムに集約させた。商品が高額なのでベトナム国内販売は難しいとのこと。
現在の職人は約125人。平均年齢は37歳で、平均勤続年数は7.5年。3ヶ月ほどで辞める人もいるが、1年続くと長くなり、10人のうち1~2人が育っていく。
「インドネシアやタイでも職人を育てていましたが、どんな人種でも同じで、モノづくりを楽しめる人、喜べるメンバーが残ります」
材料や部品の調達は、木材はアメリカ、オーストラリア、チリなどからの輸入品。塗料は約3分の1が日本からの輸入で、後は日系やベトナムメーカーからの現地調達。金具は普及品は中国、高級用は日本から輸入。段ボールは日系段ボールメーカーから購入と、調達先は様々だ。
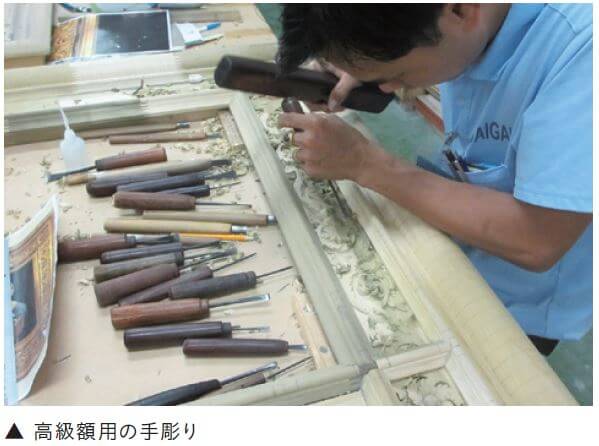
最大の額縁市場はアメリカ
世界のニーズは景気と連動
額縁の一大市場はアメリカだそうだ。人口が多く、家庭やオフィスに家族写真や絵画を飾る習慣もあるからだ。しかし、大額はアメリカに輸出していない。発注量が多すぎて生産できないのと、価格要求がシビアなので、少しでも安価な別会社があると発注が止まるリスクがあるからだ。
「また、多少のズレや汚れがあっても良しとされます。商品の価値観が違うので、大額の強みが活かせません」
ベトナム人も額縁を使うようだ。公的機関などが表彰状を贈ることが多く、一般家庭でも賞状や卒業証書を飾る習慣があり、偉人の写真を掛けることも多い。額縁メーカーはビンズン省にある国営の額縁工場が最大とのことだ。
日本での額縁のニーズは減少していると語る。表彰状を出す企業や組織、飾る家庭は減り、賞状を画像でやり取りするケースも増えた。絵画教室、学校の美術部、美術学校なども減少しており、新型コロナ禍では美術の展示会も中止となった。
「この20年ほどで業界に淘汰が起こり、日本の額縁メーカーは100人以上の大手が5~6社、家内制手工業まで合わせて100社程度だと思います」
世界的なニーズは景気動向に左右されるという。景気が良くなって所得が上がれば住宅購入者が増え、内装にこだわり、絵画などを飾る人が多くなるからだ。時流に乗るアップデートも大切になる。
「例えば、最近はカラープリントした作品を飾る人が増えているので、A4やA3サイズの額縁が増えています。また、組織編成や生産体制も時代に合った内容に変えることです」
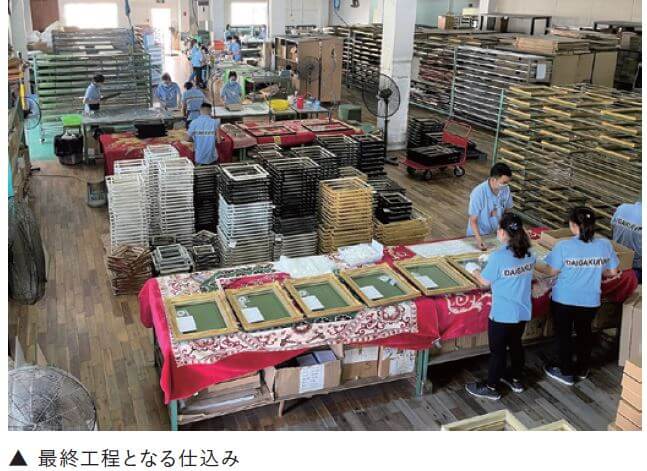
KAISUI MAREN VIETNAM
大型混み箱・水槽 海外外注から自社工場を設立
FRP製の魅力をもっと伝えたい
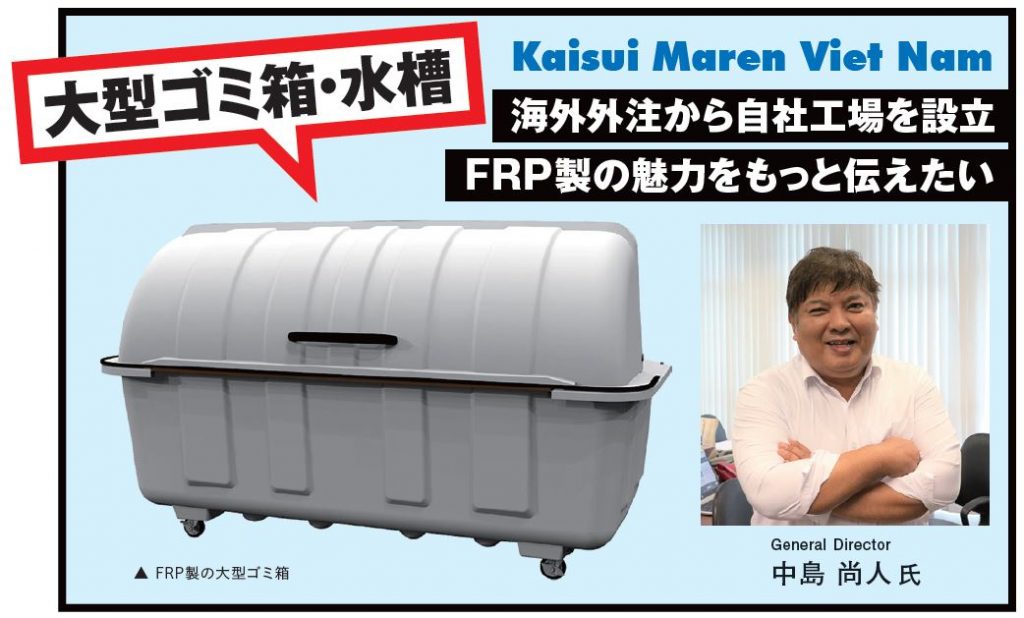
水槽メーカーが大型ゴミ箱
ラーメン店主の声がきっかけ
富山県にあるカイスイマレンは、鮮魚店や割烹などに向けたアクリルやガラスの水槽を生産していた。それが30年ほど前、営業マンがラーメン店の店主に声をかけられたことで業務用の大型ゴミ箱作りに乗り出す。
「こんな形のゴミ箱がほしいんだけど、作れる?」
しかし、材料であるプラスチックやFRP(繊維強化プラスチック)を扱う技術がなく、海外での外注生産でスタートした。ゴミを入れる箱の部分を輸入し、日本側で車輪や金具などを取り付けて販売する形だ。
「最初はインドネシア、次にフィリピンに委託して、最後は中国・上海の工場でした。ただ、人件費や外注費が高くなり、品質管理にも不安があったため、自社での生産を決めました」
そして、一部のプラスチック製商品を除き、FRP製とスチール製はすべて中国からベトナム工場に移管した。
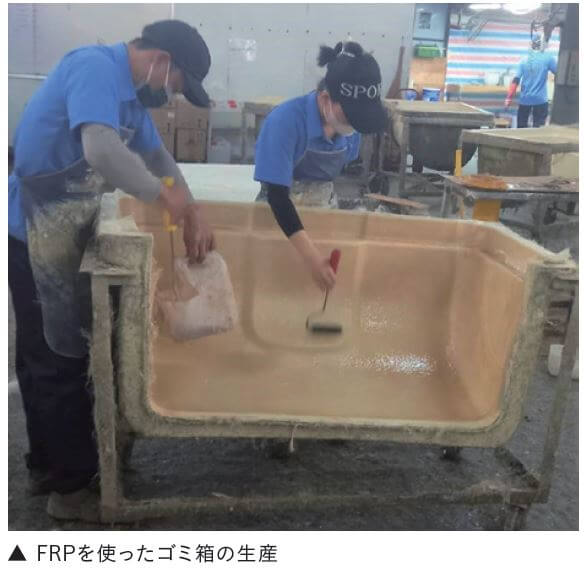
2012年頃から動き出し、生産地を社長が気に入っていたベトナムに決め、安定した気温がFRP生産に適していると南部のロンアン省を選んだ。2014年にカイスイマレンベトナムを設立し、2015年に工場が稼働する。
生産拠点を海外としたのは日本の人件費の高さに加えて、FRP生産の働き手が減っているからだ。臭いや、ガラス繊維が肌に付くとかゆみが出る人もいて、以前に多くあったFRPの工場は廃業や縮小、海外移転になっているという。
「機械化すると何億円という設備投資が必要ですが、人手の作業は単純です。弊社でも生産工程の99%は手作業です」
ゴミ箱は町内のゴミ置き場やコンビニ、病院、駅、空港などで幅広く使われており、主に幅120㎝、高さ100㎝、奥行き80㎝程度のサイズ。FRP製のほかにメッシュタイプのスチール製も作っている。ゴミ箱にはいくつかの規格があり、FRP製は約30種類、スチール製は約8種類を生産している。
こうしたゴミ箱は生産量の70%程度で、残りは水槽を生産。場所や用途によってサイズが様々なので約50種類あり、オーダーメイドも請け負っている。ゴミ箱と水槽を合わせた月産量は約1000台になる。
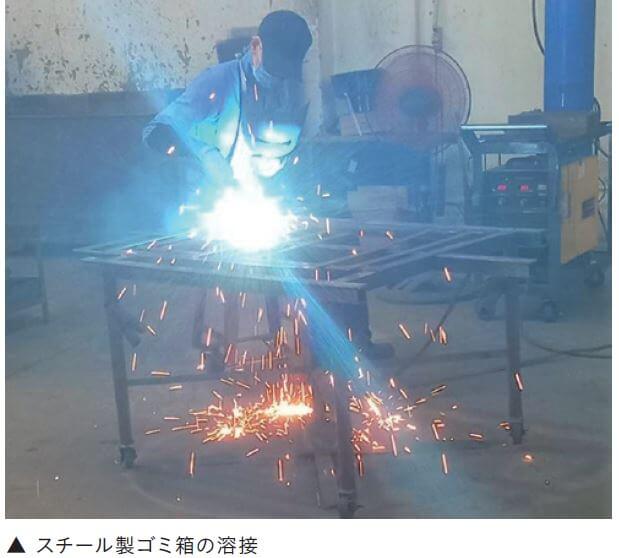
ベトナム国内販売も成長
水槽は好調、ゴミ箱は苦戦
FRPの主原料となるのは不飽和ポリエステル樹脂と、ガラス繊維でできたガラスマット。ロ-カルの商社を通じて、すべての原材料を現地調達している。
ローラーを使って不飽和ポリエステル樹脂をガラスマットに浸透させて、その後で空気を抜く。完全に抜かないと乾燥させた時にひびや割れなどの不良が出るので、作業にはスキルが必要となる。スチール製ゴミ箱には溶接技術が必要で、経験者もいるが、FRPは皆が未経験者なので覚えるのに1年はかかる。
「FRPは10人入社して残るのは1人くらい。ですから、ほかの企業よりも給与は高くしています。従業員は約60人で、FRPとスチールの担当は共に25人程度です」
FRPはプラスチックより割れにくくて耐用年数が長く、2000lなど大型サイズも生産可能。また、プラスチック製には金型が必要なので高額の初期投資が必要だが、FRP製は商品の原型があれば型取りが簡単にできる。
つまり、FRP製は高品質で、人手と簡単な材料で量産化できるのだが、商品価格はプラスチック製の5~10倍に上がる。
この価格が国内販売のネックともなった。日本輸出分は十分に生産できる体制になったと2019年から本格的に国内販売をスタート。販売数は年々上がって生産量の5%ほどに伸びたが、需要があるのは水槽のみだった。
「養殖場や水産加工工場の工業用水槽、錦鯉の観賞用水槽などで、これまで約200ヶ所に納入しています。ただ、日本でロングセラーのゴミ箱は全く売れないので、今後は商品開発が必要だと思います」
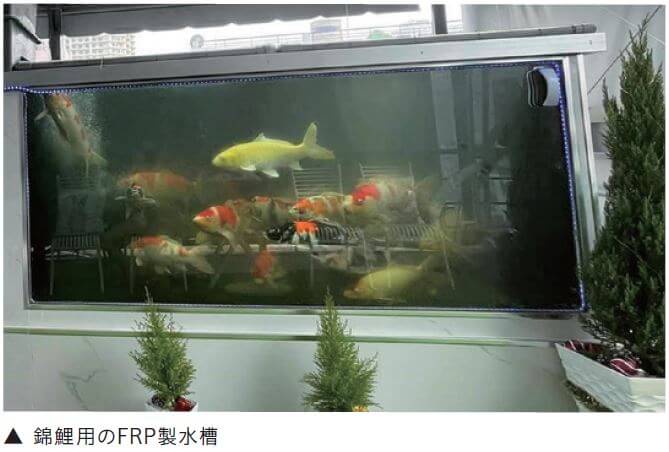
日本での大型ゴミ箱の同業他社はあっても、ベトナムに日系企業はなく、小規模なベトナム企業が多い。こうした企業の品質は良いとは言えず、劣化速度が速く、中島氏も5年程度で壊れるのを見ている。カイスイマレンの商品であれば20年ほど使われているゴミ箱も多く、半永久的に持つという。
「材料に洗浄剤を混ぜているのかもしれません。安くはなっても壊れやすいのですが、ゴミ箱ならそれで良いと考える人が多いのでしょう」
低価格メッシュタイプを開発
今後は周辺国への輸出も
日本本社の売上は上昇中で、特にスチール製のゴミ箱が売れている。これによりベトナムでの生産量も増えて、売上は毎年15~20%上昇し、新型コロナ前は7期連続で増益となった。
中島氏は2015年の設立時から赴任し、当初はベトナム人との文化の違いに戸惑った。納期を守る、設計図通りに生産するなど、日本式のルールを浸透させるのに6年かかった。ただ、そのおかげで生産体制が確立され、好業績が続けば隣接地での第2工場建設か、大きな工場への移転も視野に入ってきた。
「工場のあるタンドゥックはメコンデルタからの出稼ぎ者が多いのです。同じロンアン省なら工場を移っても一緒に来てくれると思います」
日本が好調なこともあり、注力したいのは国内販売だ。水槽は水産加工会社や養殖会社などから問合せが増えている。値段は高いと言われるが、一度購入すればリピーターとなる場合が多いので、品質の良さを説明している。
ゴミ箱は日本輸出用と国内販売用を兼ねた、低価格の新商品を開発した。日本の夏場はゴミ箱に虫が出たり生ゴミが腐ったりするが、東南アジアは年間を通して暑い。そこで、ポリエチレンのメッシュを使って風通しを良くした、折り畳みタイプのゴミ箱を作った。
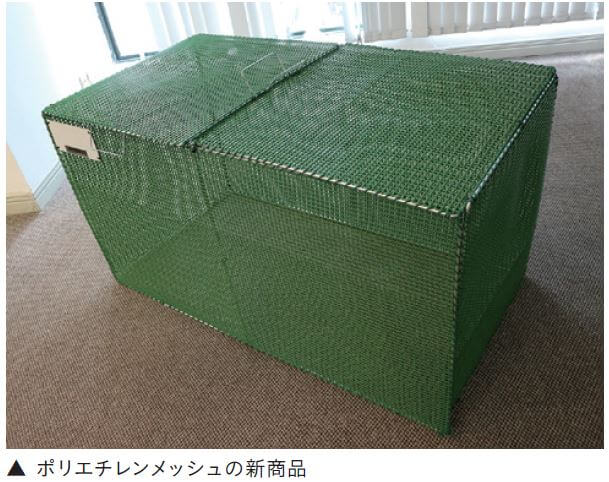
「国内販売を始めた時に、周辺国への輸出を目指した営業もしていました。まだ形になっていませんが、日本以外の輸出も手掛けたいですね」
WINE FOOD
手探りで始めたみりん原料の生産
日本だけでなく諸外国とベトナムへ
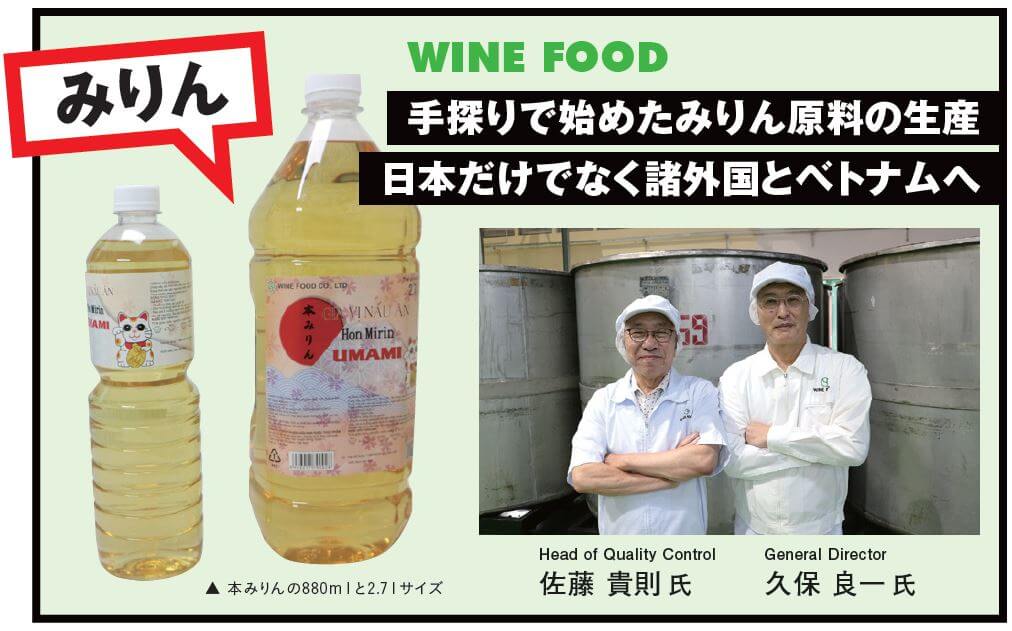
商社がみりんメーカーを設立
ブランドを高めて完成品も輸出
和食に欠かせない調味料のみりん。日本の酒造メーカーなどに本みりんの原料となる圧搾した「白酒」を生産しているのがワインフードだ。
愛知県にある親会社の大榮産業は、米、食品、酒、資材、工業部品、金属などを幅広く扱う商社。経営のリスクヘッジのため、グループ内に製造業を加えようと考えた。そんな時にホーチミン市でみりんを生産していた日系企業が撤退を決め、事業の売却先を探していた。条件は「同業他社でないこと」。
みりん作りの経験がなかった大榮産業が手を上げて、1997年に事業を継承。現在のタントゥアン輸出加工区に工場を移転した。生産の要となる技術者は前社から引き継ぎ、従業員は新しく採用した。
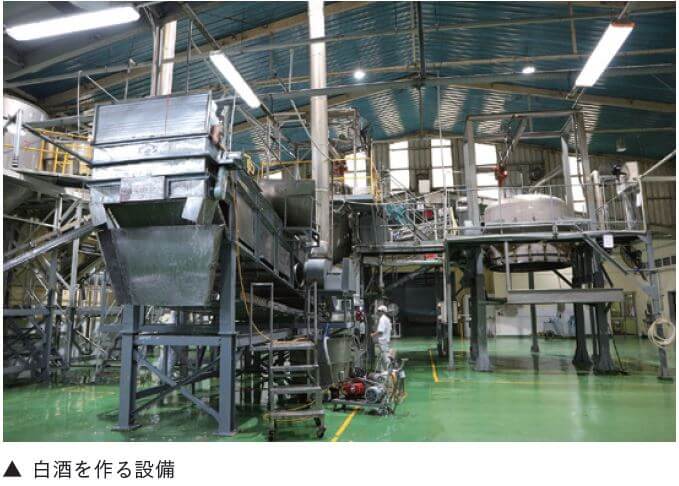
「現在は日本の大手メーカーから小規模な酒店までがお客様ですが、伝統ある会社が多いので、新規参入者の商品は使ってくれませんでした」(久保氏)
そのため、当初は塩の入ったみりんを一斗缶で送ったこともある。これは本みりんではなくみりん風調味料の原料で、食塩を入れて酒として飲めなくする不可飲処置のため、酒税がかからないメリットがある。
本みりんは江戸時代からある調味料だが価格が高く、一般家庭で使われるようになったのは昭和30年代から。現在では本みりんが主流となったが、以前は安価なみりん風調味料も市場に多かった。
「その後は徐々にブランド力が高まり、白酒の生産量が増えました。現在の年間生産量はおよそ白酒が6000kl、料理酒が500klです。この2つは作り方が違うために生産ラインは別になります」(佐藤氏)
現在、日本への輸出は65%程度。タイ、オーストラリア、ニュージーランド、カナダ、シンガポールなどへの輸出が25%、残り10%はベトナム国内販売だ。
諸外国への輸出と国内販売は20年ほど前に始めた。どちらも原料ではなくボトルに詰めた完成品で、本みりんなら一般家庭用の880ml、業務用の2.7lと18lがある。880mlサイズなどの本みりんの年間生産量は年々増加傾向にある。
「みりんは日本独自の調味料ですから海外やベトナムに住む日本人向けが主で、ベトナムでは日本の食材店とオンラインで販売しています。ベトナム市場に参入してはいますが、まだまだ認知度が低いです」(久保氏)
日本と違う環境に試行錯誤
原料は輸入と国内から調達
みりん原料の生産を未経験から始めたわけだが、日本での作り方は参考にしても、そのままでは使えなかった。なぜなら、米などの原料や水、工場の温度や湿度が日本と異なるからだ。
例えば、日本での麹作りは寒い環境であることが多いので、室内の温度を上げ、加湿装置で湿度を高めた麹室(むろ)などで作る。一方、ホーチミン市は年間を通して温暖なのでその必要がなく、逆に菌が育ちすぎるので冷却設備が必要となる場合もある。
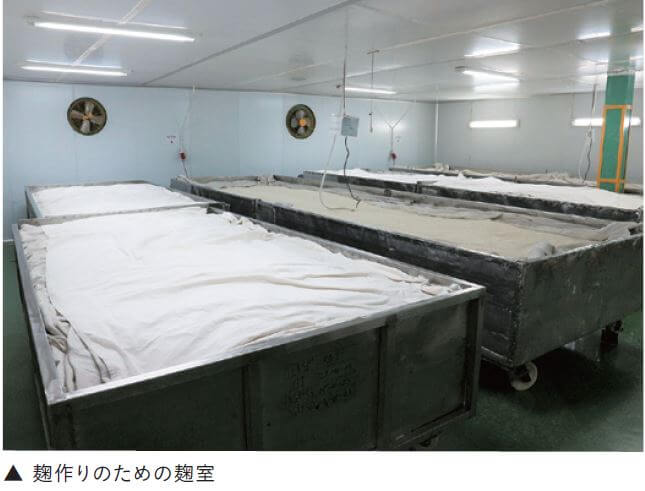
「前例がなかったので製法を変えながら、試行錯誤で覚えていきました」(佐藤氏)
完成品の本みりんはどう作るのか。まず原料となる米麹、精米、精製アルコールを職人が混ぜる。これを「仕込む」と言い、工場内には精米機や蒸気窯があり、アルコールは200klのタンクで保存している。いかに均一に素早く混ぜるかが大切で、技術と経験が必要になるそうだ。
これを熟成タンクで熟成させた後、圧搾機で圧をかけて搾る。搾られたみりんを糖類等と混合させて、濾過と殺菌を行う。最後に輸出用のタンクコンテナや市販用のボトルに充填して完成だ。ここまで30日が目標で、出荷まではおよそ45日かかる。
「アルコールと糖類はベトナム、米はベトナムとタイ、ブドウ糖はフランスやイタリアから輸入しています。麹は日本にしかないので日本から種麹を輸入しています」(久保氏)
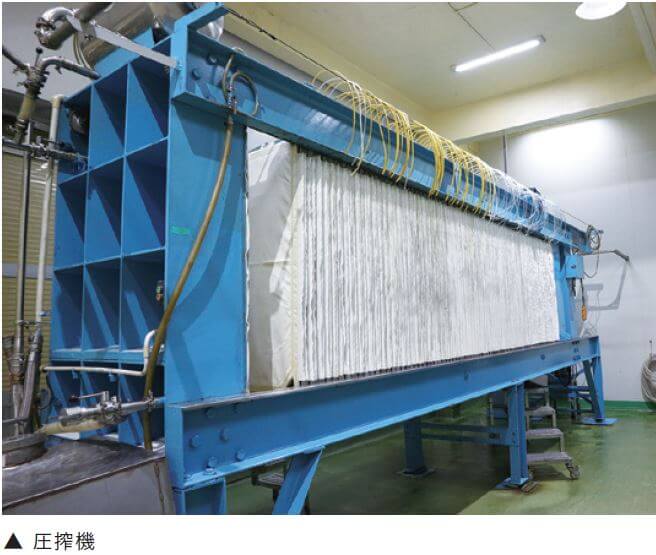
焼酎、甘酒、調味料の塩麹
本みりん以外の商品も開発
佐藤氏は2007年から現場責任者をしており、以前はみりんを作る職人としてみりん醸造メーカーで働いていた。現在は30人ほどが生産現場で働き、製造マネジャーはベトナム人が務める。日本で研修を受けたスタッフも在籍している。
「一人前になるのに3年は見たいですね。日本のように原料や気候が一定していると覚えが早いのですが、これらが安定していないので時間がかかるのです」(佐藤氏)
十数社ある日本の顧客企業に合わせて、使用する米や麹の量、度数、リッター数などを変えている。一般的にベトナム人は変化を嫌うといわれるが、こうした作業から変化に対応できるスタッフが育っているという。
「大切なことは日本と同じですが、仕事をする仲間の気質が合うことです」(佐藤氏)
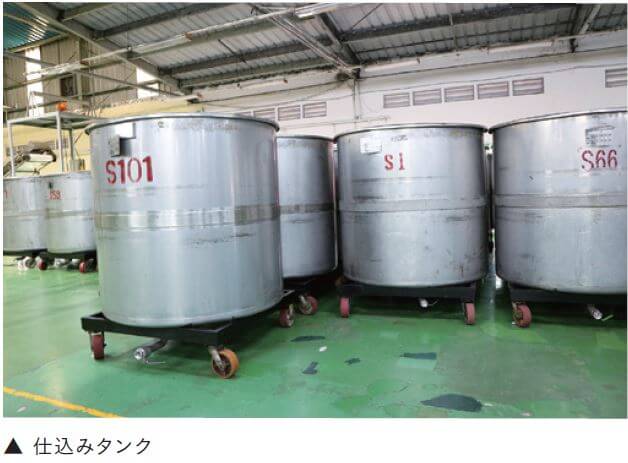
日本のみりん市場は売上が落ちているそうだ。日本のメーカーがワインフードにその原料を求めるのも、設備投資をしにくいためだろう。みりん、塩、しょうゆなどの基礎調味料だけではなく、たれ、つゆ、各種ソースなどの加工調味料を開発するメーカーも増えている。
そのため、同社は他国への輸出と国内販売に力を入れる。輸出は日本食ブームの欧州諸国へ、和食レストランに完成品の販売を考えている。ベトナム国内向けには、みりんを使ったレシピの配信、展示会での試食会、スーパーでの実演販売などでアピールしている。
みりんや料理酒以外の商品も開発しており、これまでに調味料の塩麹、麹を使った甘酒の「甘酒美人」、甲類焼酎の「ZERO」などを販売してきた。
「料理にみりんを使うのはベトナム人には手間がかかることもあり、商品開発は欠かせません。そのために6年前にR&D室を立ち上げて開発を続けています」(久保氏)