ベトナムで工場の自動化が進む。デジタルデータの活用による生産の効率化、無人搬送車による正確で素早い搬送、自動機による確実な作業や検査……。各企業はどの工程を自動化して、生産をどのように進化させているのか。
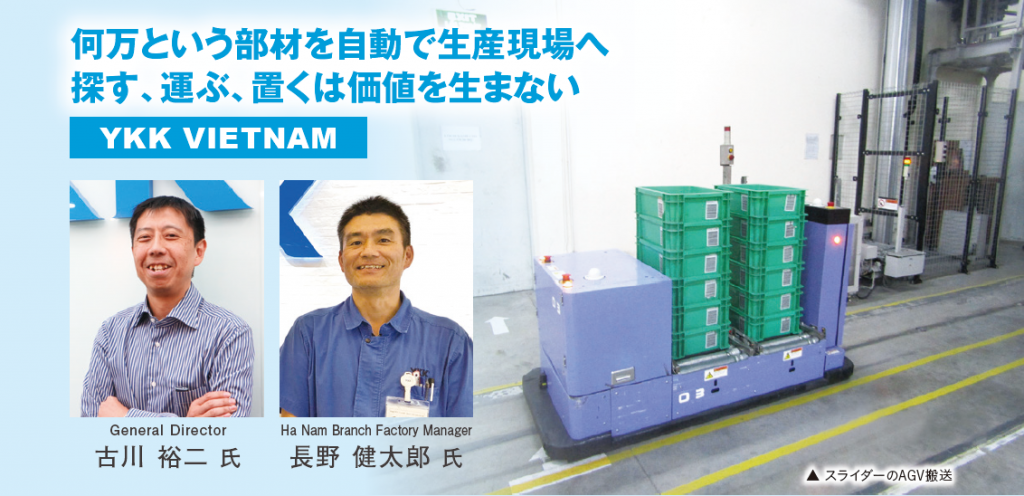
グループ上位3位の生産量
主力工場はニョンチャック
1998年5月に設立されて今年25周年を迎えたYKKベトナム。1999年に南部ドンナイ省のアマタ工業団地にビエンホア工場、2012年は同省のニョンチャック工業団地に第1期、2015年には第2期の工場を竣工した。
2016年にビエンホア工場からの移設を完了してニョンチャック工場を主力工場とし、2019年には北部に進出してハナム省のドンバンIII工業団地にハナム新工場を竣工した。
「ハナム工場は2023年4月に増築に着工しました。2024年1月の完成を予定しています」(長野氏)
生産しているのはYKKの主力商品であるファスナー(ファスニング製品)だ。両工場で2022年に生産されたファスナーは約10億本。世界72の国と地域で事業展開するYKKグループの中で、ベトナムは上海、バングラディシュに並ぶトップ3の生産量を誇る。
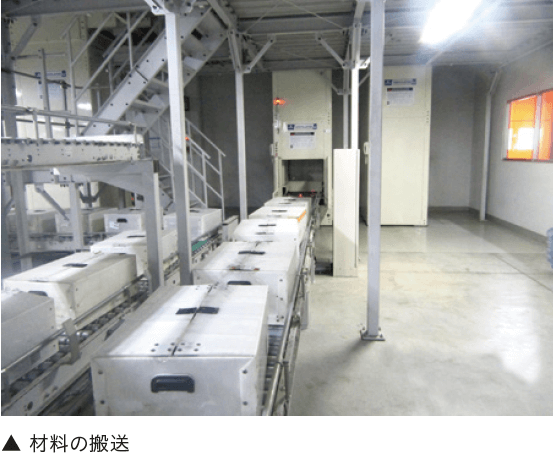
YKKの世界進出はその地の顧客に商品を提供するのが基本で、ベトナムでは国際的なアパレルメーカーやシューズメーカーなどの生産工場を中心に商品を納入している。
材料からの一貫生産工場であるニョンチャック工場は3つの建屋から構成されており、その延床面積は約12万㎡、約2000人が働く。
第1棟ではファスナーを開閉させるスライダーを生産。亜鉛合金からダイキャスト、組立て、塗装やメッキなどの表面処理も自社で行う。
第2棟はファスナーの繊維部分を生産。ポリエステルの糸から織機を使ってファスナー用のテープを生産しており、そのテープにファスナーの噛み合わせ部分となるエレメントを取り付ける。
ファスナーの種類によってエレメントは異なり、金属部品の植え付けや、樹脂の射出、ポリエステル成型品の縫工などがある。ファスナーの染色も自社で行っている。
第3棟ではこれらの部材を組み合わせて最終商品であるファスナーを生産。YKKでは各製造工程の製造機械全てを日本の本社工場で自社開発、設計、製造している。世界各国で材料からの一貫生産と自社開発の専用機を用いることで、グローバルで統一された高い品質の商品の生産が可能となっている。
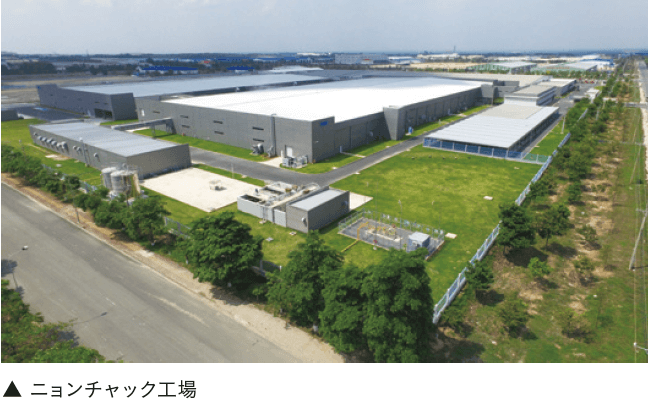
品番、自動搬送車、コンベア…
受注内容の入力も自動化
ファスナーは基本的に受注生産だ。商品数はスライダー、テープ、エレメント、寸法の組合せの掛算となり、色やサイズの種類も豊富なので、最終的に何万何十万という品数になる。また、顧客の要望は多種多様であり、ますます多品種小ロット化が進んでいる。
各工程で生産される部材は倉庫の棚に分けられ、当初は台車などで人が生産現場に運んでいたが、顧客の納期短縮要望の高まりや生産量の増加により、人的対応では限界となっていた。
「そのため自動化を検討し、ニョンチャック工場の第2期からFAや自動倉庫などが導入されました」(古川氏)
現在のニョンチャック工場では各部材は品番で管理され、システムから指示を受けたAGV(無人搬送車)が指定された棚から材料を移動させ、あるいはコンベアを使うなどして、部材を生産ラインにシームレスに搬送している。
「特殊な形状のスライダーなど一部の仕上げ生産は手作業ですが、表面処理などを含めて生産も自動化を進めています」(古川氏)
自動倉庫は立体的な構造となっており、人の手の届かない高さまで活用できるので、面積や空間を有効に活用できる。また、生産された商品も自動倉庫を活用することで、その後の梱包作業も効率化された。
こうした自動化を支えるのはYKKグループ内で開発したシステムの活用で、グローバルに展開している。また、YKKベトナムは業務プロセスでもRPA(Robotic Process Automation)を2018年から導入。煩雑な事務作業の自動化を図っている。
顧客からの注文書はWord、Excel、PDFなどに分かれ、そのフォーマットも各社で異なる。メールだけでなくファクスや電話での注文もある。従来は従業員が発注内容を基幹システムに入力していたが、それを自動化したのだ。
「受注件数が多いのでオーダーを受け取って生産開始するまで数日必要でしたが、RPAで大きく短縮されました」(古川氏)
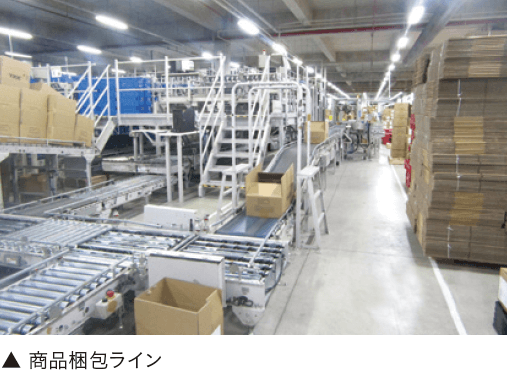
ハナム工場は自動化の最中
作業に集中できるメリットも
ハナム工場はニョンチャック工場同様ファスナーを生産しており、約14万㎡の土地に建屋の延床面積は約5万1000㎡、約650人が働く。
立上げ時は品数が少ないことからマテリアルハンドリング(マテハン:材料・部品などの移動や搬送)は手作業が中心だったが、2022年には約2億8200万本と生産量を増やし、今後の増産も見込んで自動化に着手した。増築中の工場の面積は約4万㎡となる予定だ。
「今まさに進めていますが、自動化は大変です。手動での作業や工程のどこに問題や課題があるのか。そこから調べ始めました。自動化は手段の一部ですので目的ではありません。将来のことも予測して施策を考えています」(長野氏)
このように自動化をいきなり導入するのは難しい。また、手当たり次第の自動化も勧められず、人が介在すべき作業を残すことも必要だという。ただ、「探す」、「運ぶ」、「置く」などの価値を生まない作業はコストと時間を抑えるべきで、付加価値を生む作業とは「加工」と語る。
ニョンチャック工場のように主にマテハンを自動化して、年間生産量を現在の約3億本から倍の6億本とするのが目標だ。
また、YKKグループではサステナビリティに注力し、材料にリサイクル材を用いるなどしているが、YKKベトナムは生産工程のトレーサビリティを推進している。ラベルのバーコードなどを読み取ることで、材料の購入履歴、生産日、ロット数などを把握できるシステムの構築で、顧客に安全と安心を届けたいという。
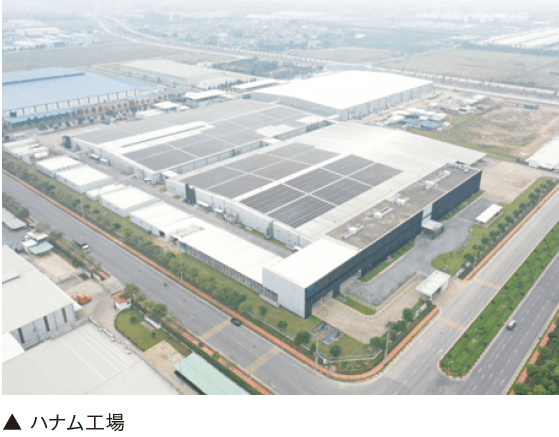
「自動化が進むと従業員の負担が軽減され、やるべき作業に集中できるのも大きなメリットです。生産を伸ばし、顧客満足度を向上させるためにも、自動化を加速させたいです」(古川氏)
「第2期の工場を完成させて早く軌道に乗せたい。従業員の増員、商品供給力の増強によってベトナムの繊維産業に貢献していきたい」(長野氏)
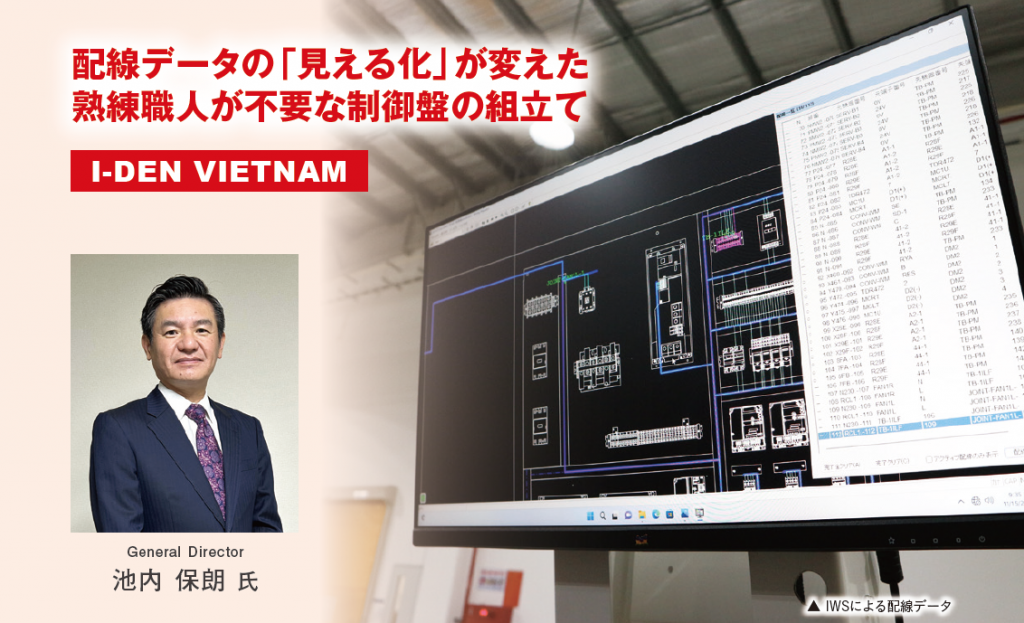
技能実習生がきっかけ
レンタル工場から自社工場
アイデンは石川県金沢市にある、機械や装置を電気制御する制御盤のメーカー。各種工作機械用、物流設備用、電池製造ライン用など多様な用途とサイズの制御盤の、設計、板金、塗装、組立て、検査までを行う。一般的な制御盤の生産では板金や塗装を外注することが多く、一貫生産体制は同社の大きな特徴となっている。
2007年竣工の第1工場と2017年竣工の第2工場を持ち、受注増から新工場を考えた。一方、人材の獲得が難しくなり、ベトナム人の技能実習生を採用したところ、皆が真面目で勤勉に働いた。
「制御盤の生産はコツコツとした手作業が多く、ベトナム人に向いていると思いました」
ただ、技能実習生は3年で帰国してしまう。そして、帰国後にスキルを活かせる職場がないとも知って、新工場をベトナムに作ると決めた。
2017年にアイデンベトナムを設立し、ドンナイ省ロンドウック工業団地のレンタル工場からスタート。同年4月に生産を開始し、当初は年末の出荷を予定していたが、IWS生産(後述)と順調な作業で7月に出荷できた。
板金と塗装を外注した組立て生産だったが、好調な滑り出しもあって、日本と同様の一貫生産にすべく自社工場を計画。工場長が見つけたのがドンナイ省のザンディエン工業団地で、2019年11月にベトナム工場が竣工した。敷地面積は約1万500㎡、工場の延床面積が約4100㎡で、工場拡張用に約2000㎡がある。
日本と同様にベトナムで導入したのが、自社で内製したIWS(iDEN Wiring Solution)というシステムを使った生産方式だ。
制御盤の組立てには電気学科を卒業するような電気の専門知識が必要となる。回路図を読み、電気の容量から電線の太さを判断するなどだ。こうした知識や経験を不要としたのがIWSで、2013年頃から活用している。
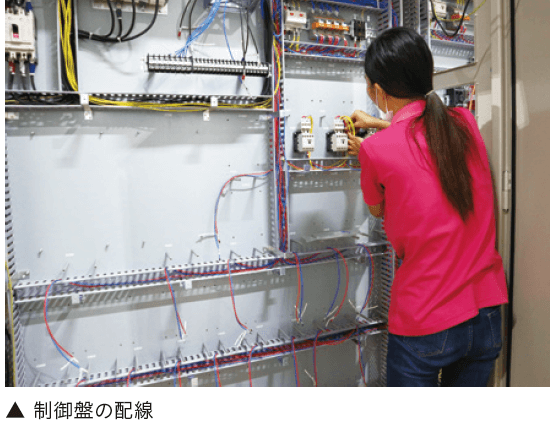
配線データをモニター表示
ベトナムでも一貫生産体制
IWSは設計で作成したCADデータを活用して、制御盤の組立てに不可欠な部品の配置図と回路図の図面情報を融合させる。ここから1つの配線データを作り出し、この「仮想配線」をモニターに表示して、作業者はそれを見ながら組み立てる。
「電線の長さや太さ、配線順、配線経路、配線場所などがすべてモニター表示されるので、誰でもベテラン職人と変わらぬ配線が可能となります」
この配線データを転送すればどこでもIWS生産が可能となる。ベトナムでも技能実習生が主な設立メンバーとなり、現地採用のベトナム人にIWSでの組立てを教えていった。だから出荷を早められたのだ。
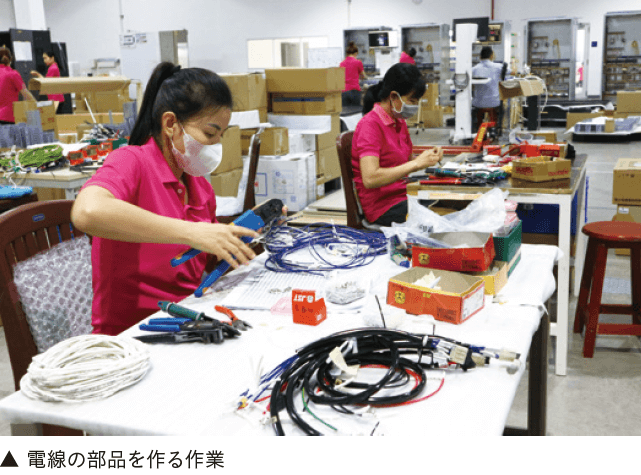
配線データによる配線の数値化や見える化で、アイデンは制御盤内の1本単位の電線の自動生産も実現した。自動電線加工機を24時間稼働することで、月産約2万本を加工している。ここでも熟練作業者による機械加工が不要となり、納期を大幅に短縮できた。
「設計段階で配線の本数や使用部材の詳細がわかるので、適正な原価計算や生産量の即時調整ができます。機械化で圧着不良や印字ミスが削減できて品質も向上します」
ベトナムでは人件費の安さから自動電線加工機は導入せず、電線の切断のみを自動化しているが、日本とほぼ同じ一貫生産体制を確立させた。設計は日本が担当する日系メーカーが多い中、アイデンベトナムでは日本で5年の経験を持つベトナム人CADエンジニアなどが設計している。
EPE企業として日本に輸出しているため、納期の長い製品を優先的に生産しているが、品質は日本と同じだ。制御盤の性能やサイズなどで様々だが、設計から出荷まで約2ヶ月、図面があって板金から出荷までが約1ヶ月という。
「塗装は粉体塗装と溶剤塗装をしていて、塗装だけの受注があるほど技術力には自信があります」
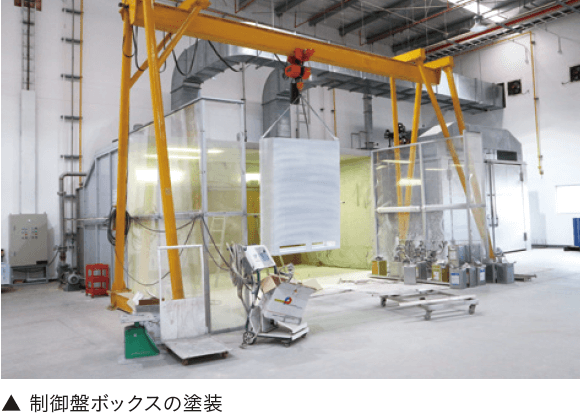
増産はベトナム工場に期待
今の課題は生産性の向上
2019年11月の工場完成後から新型コロナが流行し、本格的な稼働は今年から。だが、新型コロナの影響で中国からベトナムへの工場移管、チャイナプラスワンでベトナム工場などが増加し、制御盤の受注が増えている。
ベトナムに生産拠点があるならと取引が始まったケースもある。中国生産でなくベトナム生産なら安心でき、価格が抑えられていることも魅力のようだ。部品は日本本社からの輸入が多く、板金用の鉄材は主に日系企業から購入しているが、安価な人件費と生産効率で低価格を実現した。
日本では人手不足などで増産が難しく、従業員約70人のベトナムが期待されている。現在のグループの生産割合はベトナムが2割程度と余力があり、工場の3割程度は空きスペースで、将来は増設用の土地もあるからだ。そこで課題となるのは生産性の向上で、仮に組立ては早く覚えても、満足できる作業になるまで半年や1年はかかるそうだ。
そのため日本とベトナムで作業者単位での作業時間の履歴を取得し、統合して全体の進捗管理をしている。以前は熟練作業者の感覚で1日、2日などと決めていたが、工程単位の作業時間が把握できて、適正な時間がつかめるようになった。
「生産性を向上させないと生き残れません。ただ、日本のお客様が驚くほど品質は高いですし、ベトナム人は優秀だと思います」
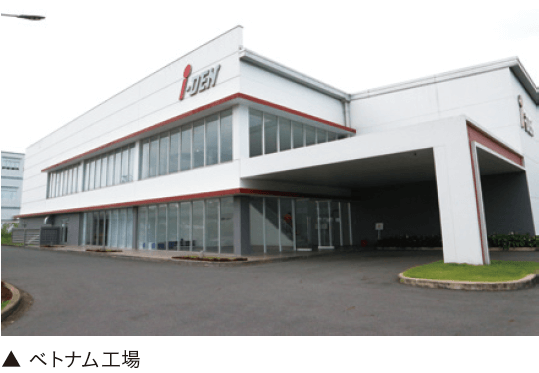
アイデンベトナムでは事務所と食堂を外光が差し込むガラス張りにし、工場は埃などが入らない外気を遮断した無窓の完全空調。チーム体制を重視した「ワンチーム」を掲げており、給与や待遇を安定させた終身雇用に近い人事制度としている。従業員の定着率は高いという。
「今後はさらに自動化も進めていき、ベトナムでの技術向上、産業の発展に貢献できるよう努力していきたいと思っています」
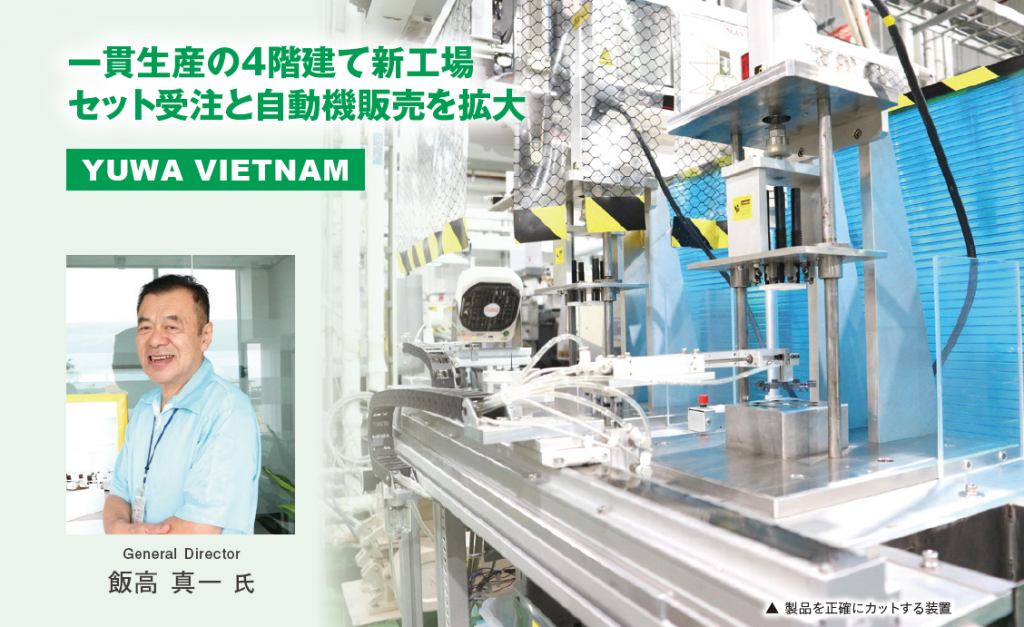
「点から面」へ事業を展開
2024年1月に新工場完成
小型精密プラスチック部品の金型製作から各種成形、製品の組立てまでの一貫生産をするユウワベトナム。スマートフォン用部品、EV用バッテリー関連部品、医療用検査機器部品、車載のハーネス用部品など多彩な製品を生産しており、主要顧客は電子部品、車載用部品、医療機器など当地の日系メーカーだ。
2009年に南部ビンズン省のVSIPⅡ工業団に第1工場を竣工。約9000㎡の土地に建屋の延床面積は約1万1000㎡。主に金型加工用の工場で、そのための恒温室では25±0.1度の温度管理が可能だ。
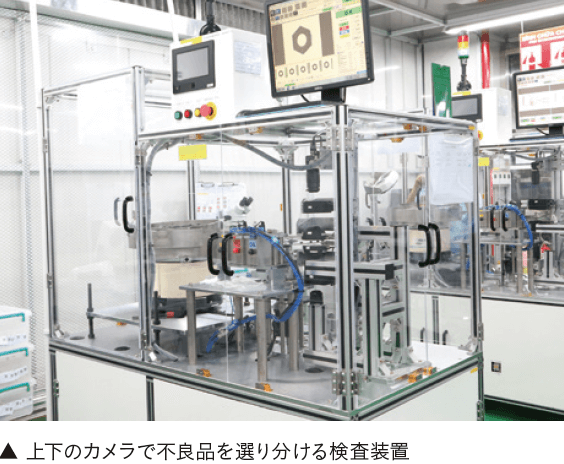
2018年には第2工場を同工業団地に竣工。2万2500㎡の面積で建屋の延床積は約1万4900㎡。主にプラスチック成形用の工場で、24±0.3度の温度管理が可能な成形用恒温室にクラス100,000の成形エリア、ほかにクラス10,000というクリーンルームを持つ。
2021年には同工業団地のレンタル工場で第3工場を稼働。クリーン成形の第2工場に対して、金属などのインサート品と樹脂を一体にするインサート成形用の工場だ。
「新工場を作る予定でしたが、お客様が完成まで待てないとレンタル工場で生産を始めました」
その新工場は第2工場の隣接地に建築中で、2024年1月の完成予定。約4500㎡の土地に延床面積が約1万8000㎡の4階建てとなる。1階は半分が成形用、残り半分は金型部門、2階は金型設計、試験、測定用、3~4階は組立て工場で、新工場内で金型設計から組立てまでを完結させる。
「従業員が約1300人となり、現在は点から面へと事業を広げています。そのための新工場でもあります」
近年は金型設計から成形による部品の生産に加えて、塗装などの加飾、関連する複数の部品の生産、その後の組立てなどの依頼が増えてきた。複数の工程をまとめて請け負う「セット受注」は売上の増加だけでなく、各部品の使い方がわかるために生産効率の上昇や品質の向上につながっている。
「仮に10の部品の生産を3社に分けた場合、どこかに不良品や納期遅れが出ると全体のスケジュールが滞りますし、組立てにも手間がかかる。ならば一括委託のほうが確実です」
この発注方法はサプライヤーの高い技術力や生産能力が前提となるが、ユウワベトナムには新型コロナ明けから依頼が増えており、逆にセット受注の話を向けると興味を持たれるという。「面」への事業が拡大している。
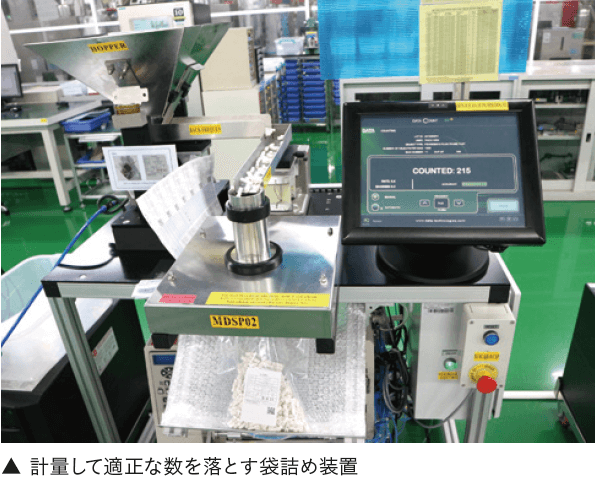
自動機の開発・販売
350tまでの射出成形機
もうひとつの新規事業は、組立て用や検査用など各種自動機の製造・販売だ。同社では以前から自動機を内製して工場で使用しており、2019年から自動機の外販事業を始めた。当初は5人だったチームが現在は50人規模に増えている。
自社工場で使っている自動機をいくつか挙げる(写真参照)。完成した製品をカメラで複数の方向からチェックする検査装置。製品を計量して適正な数を落とす袋詰め装置。カメラで検査した部品を複数の箱に分け入れる装置や、成形した製品を正確にカットする装置などもある。
「お客様用では2つの成形機から部品を取り出して自動溶着し、完成した製品を箱詰めする自動機などがあります」
自社用の自動機は担当するエンジニアたちが考案する場合もあれば、現場でのヒアリングから工夫を凝らす場合もあり、設計から完成までおよそ3ヶ月。自動機の製作だけでなく、部品メーカーとしての経験とノウハウがあるからこそ、顧客の望むマシンが作れるという。
このように新工場はセット受注と自動機外販のための建設となった。これまで型締め力最大200tまでの射出成形機が最大クラスだったが、新工場では最大350tとなる予定だ。1ランク大きな成形機と金属加工機を導入して、セット受注を見越している。小型部品や大きなハウジング(筐体)を生産するセット受注を増やすつもりだ。
「ベトナムに合計約220台ある成形機は新工場にもう100台入れて合計320台体制、金型加工機は約110台あり新工場に100台追加して合計200台体制を計画しており、5~6年をかけて増やすつもりです」
新工場でのキャパシティが埋まったら、東南アジア最大級のプラスチック製品生産拠点になるだろうと自負する。
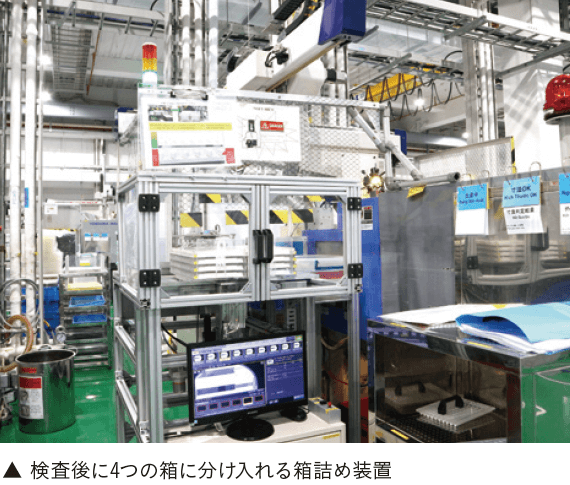
ITやシステムでの自動化
中国からの移転がチャンス
自動機の利用だけでなくシステムによる自動化も進める。現在は設計部で図面を作成した後、放電加工機やワイヤー加工機などのマシンを動かすプログラムを組んでいる。ミスもあり得るし時間もかかるので、CADの設計データを元にプログラムを生成する仕組みに変える予定だ。
「加工機により種類や年代が異なるので全てを一度にはできませんが、新工場で何台かずつ始めたいです」
また、製品はバーコードで管理しており、部品単位で生産管理を見える可している。A、B、C、Dの部材でZを作るなら、どの部材がどの工程にあり、Zはどのくらい生産されているかなどがわかる。ただ、金型、成形、組立ての3部署それぞれで管理しており、ソフトがこの3工程で連動していない。新工場では一括管理できるようにする予定だ。
新型コロナ明けから、中国からベトナムへの工場移転が多くなり、同社の顧客である日系メーカーも増えている。こうした企業に加えて、欧米系企業からの海外向け生産の発注も増えており、セット受注や自動機販売のチャンスと見ている。
ただ、近年ではベトナムでの人件費が上昇し、工場のエンジニアも高給になっている。大幅な円安が続いた結果、特にEPE企業はベトナムで生産するコストメリットが出しにくくなっている。
「世界的な不況や減産もあって『次の活況』が見えない状態です。ただ、弊社は自動化や設備に投資をして、『次の活況』の先取りをしていくつもりです」
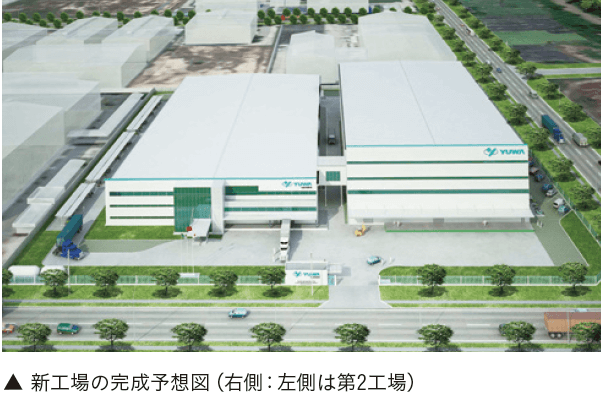